These products are the very nice. Suntime Precision Mould spent 4.5 weeks for manufacturing.
It is for car tail lighting with surface A1 polishing.
The main difficulty is tooth profile and how to control the warpage.
The tooling process includes CNC machining, wire-cutting, EDM, grinding, drilling and polishing, etc,.
We provided service for the famous car brand such as Bentley, Mercedes-Benz, BMW, Audi, Volvo, Toyota, Honda and so on.
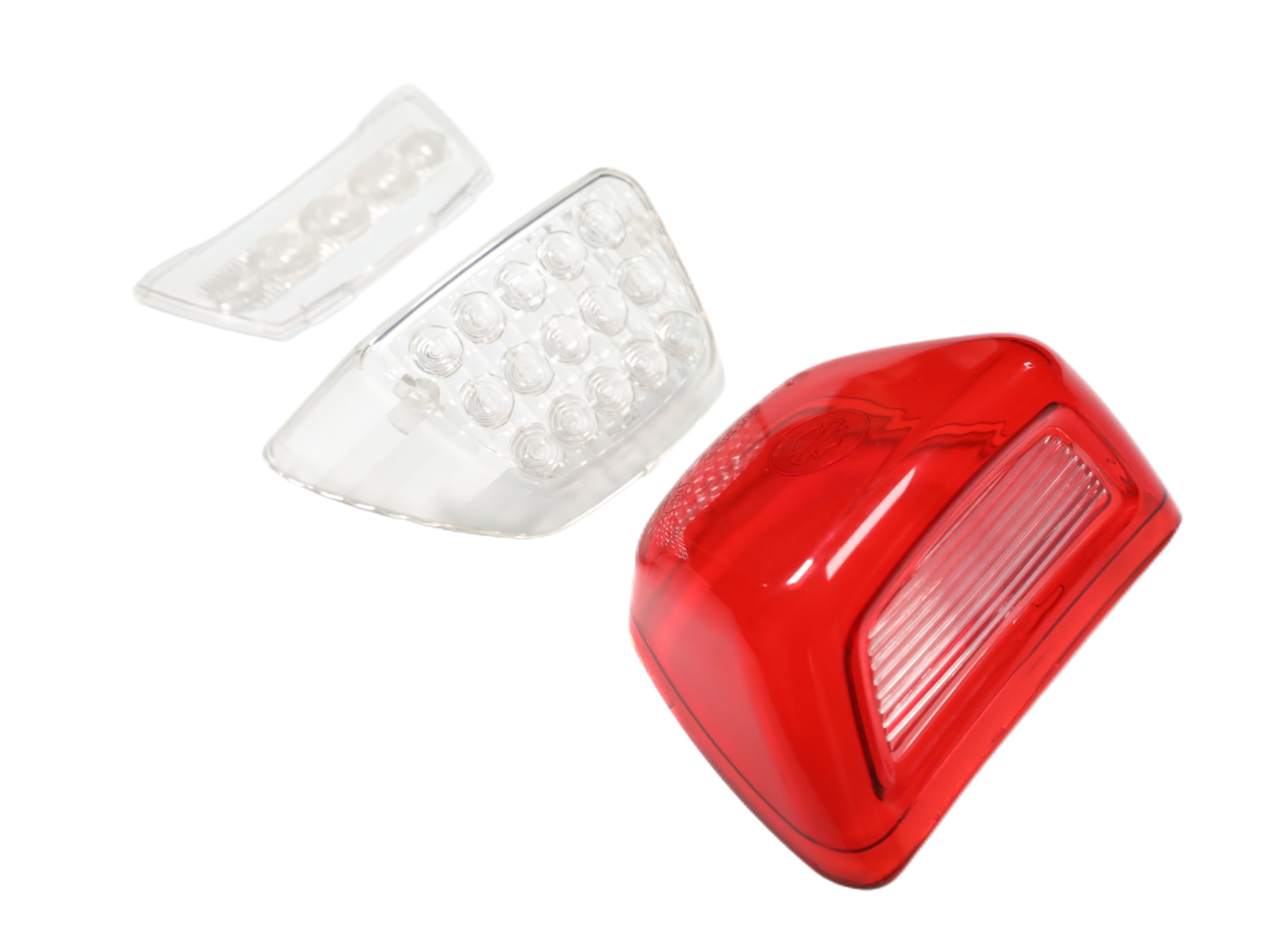
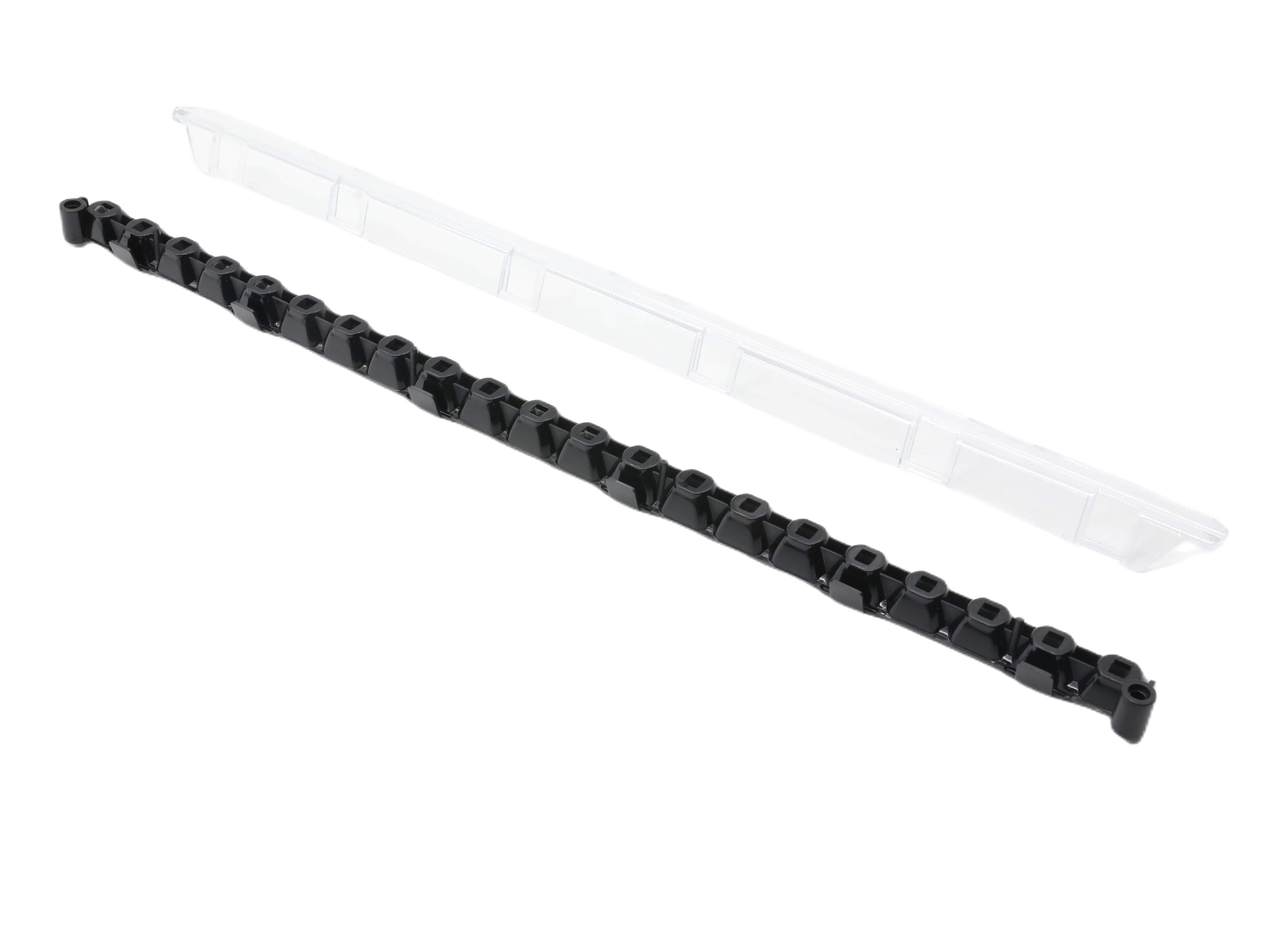

Appliance and Type | Automotive lighting lens from plastic injection family mould | |||||
Part name | Housing and Lens (Automotive lighting) | |||||
Resin | PC/ ABS and PMMA | |||||
No. of cavity | 1+1 cavity family mould | |||||
Mould Base | LKM S50C | |||||
Steel of cavity&Core | P20 | |||||
Tool weight | 950kg | |||||
Tool size | 600X450X450 | |||||
Press Ton | 160T | |||||
Mold life | 500000 shots | |||||
Injection system | Cold runner mould Edge gate | |||||
Cooling system | 110 ℃ | |||||
Ejection System | Strpper plates, ejector pins | |||||
Special points | Products are for automotive lighting lens and housing, surface is A1 polishing. | |||||
Difficulties | tooth profile takes difficulties for machining and polishing. Need to control well for warpage. | |||||
Lead time | 4.5 weeks | |||||
Package | Stored in Suntime factory for production | |||||
Packing items | / | |||||
Shrinkage | 1.005 | |||||
Surface finish | A-1 | |||||
Trade terms | Exwork | |||||
Export to | UK |
We are ISO 9001 certificated
More than 40% business for automotive parts
From single cavity simple interior part to car tail lighting parts
Served brands includes: Bentley, Mercedes-Benz, BMW, Audi, Volvo, Toyota, Honda and so on.
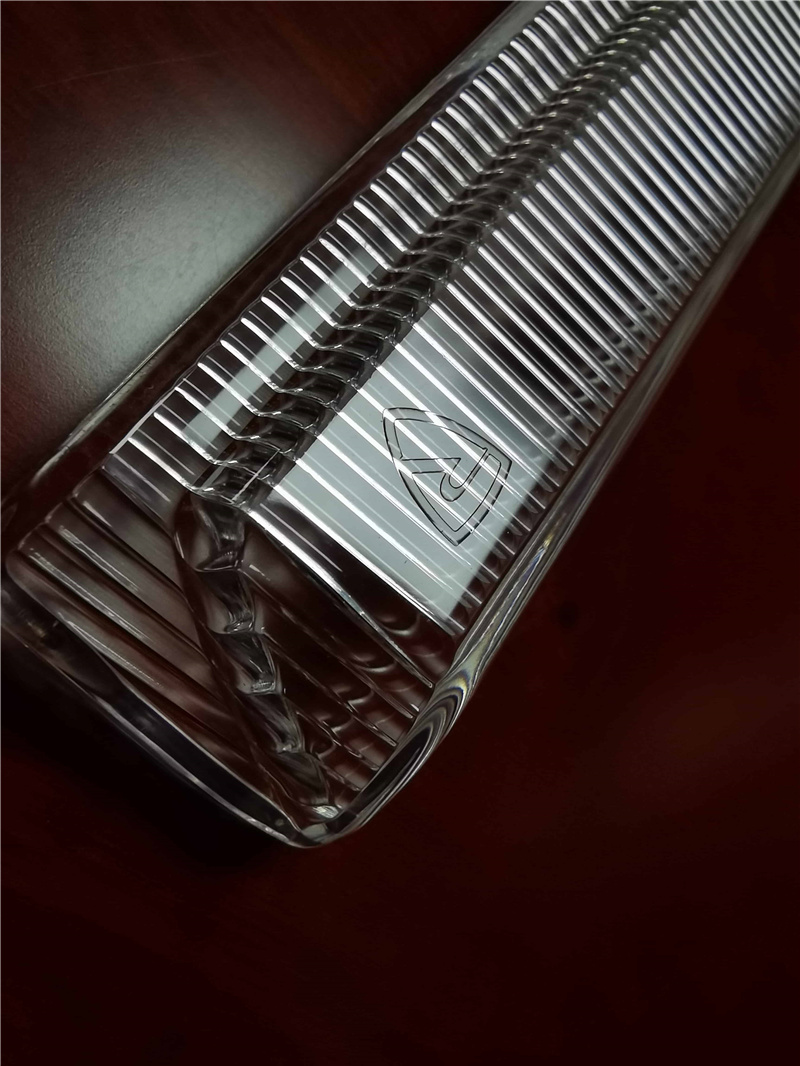
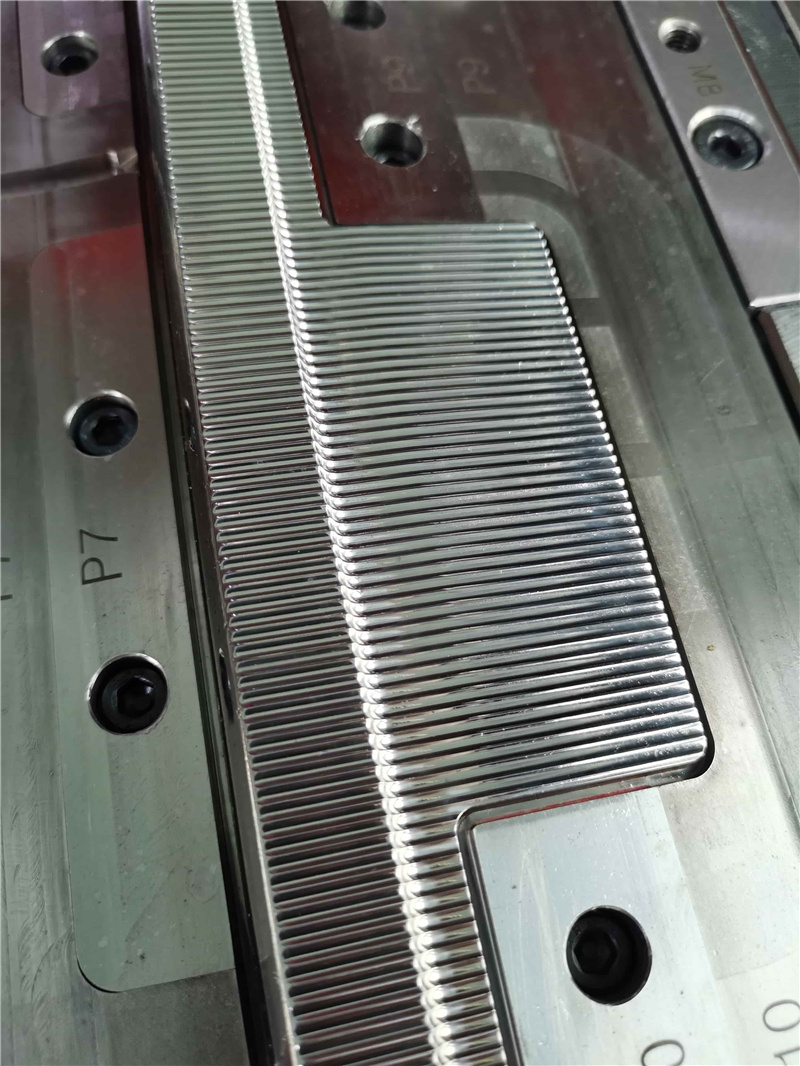
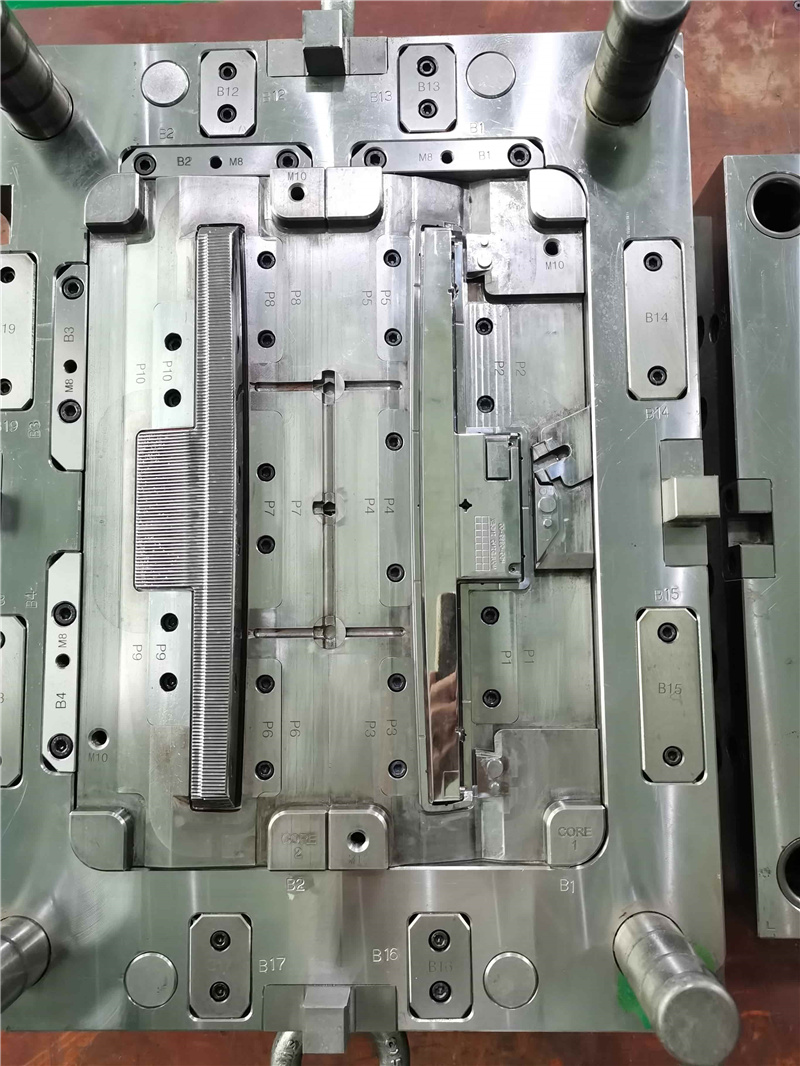
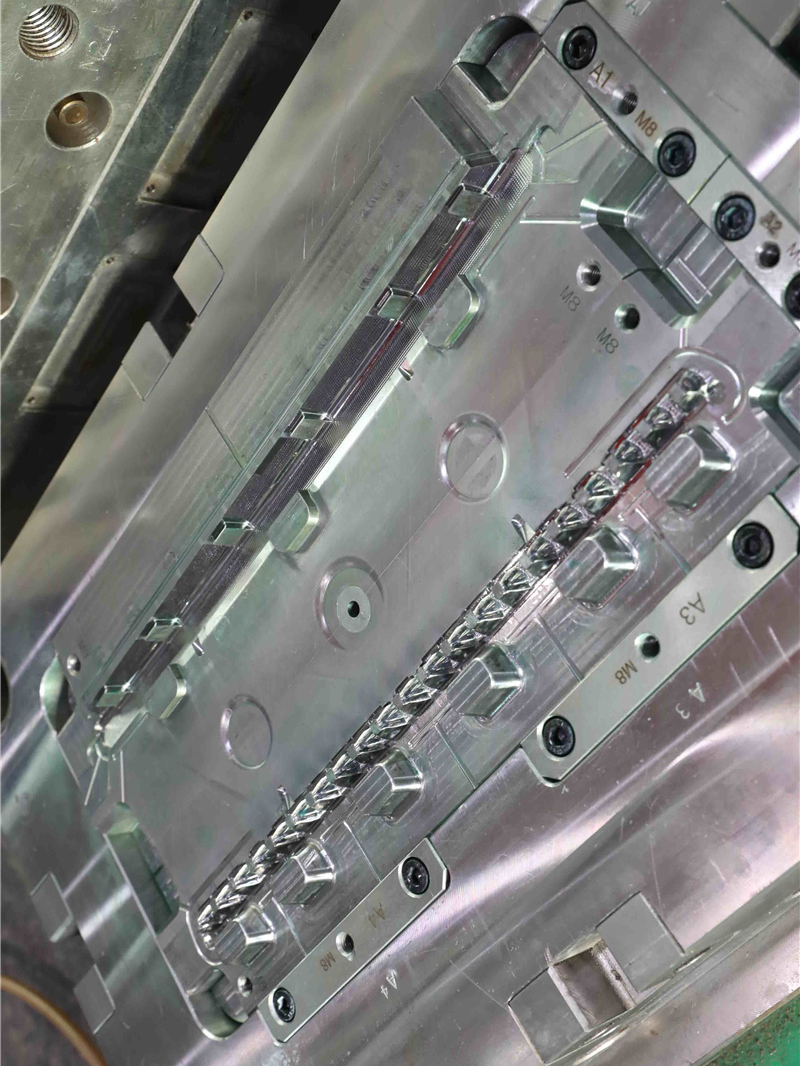
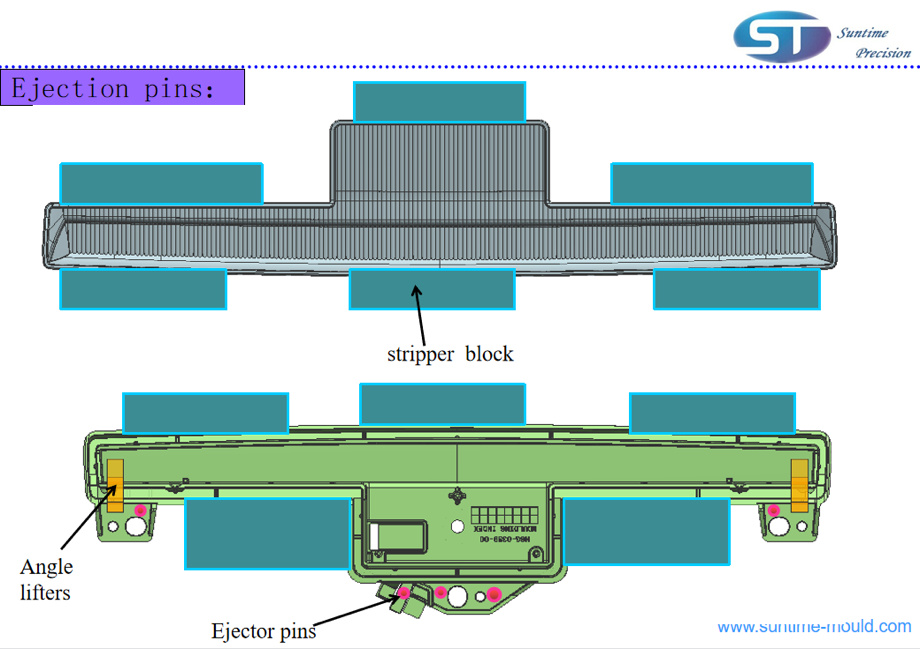
DFM Analysis
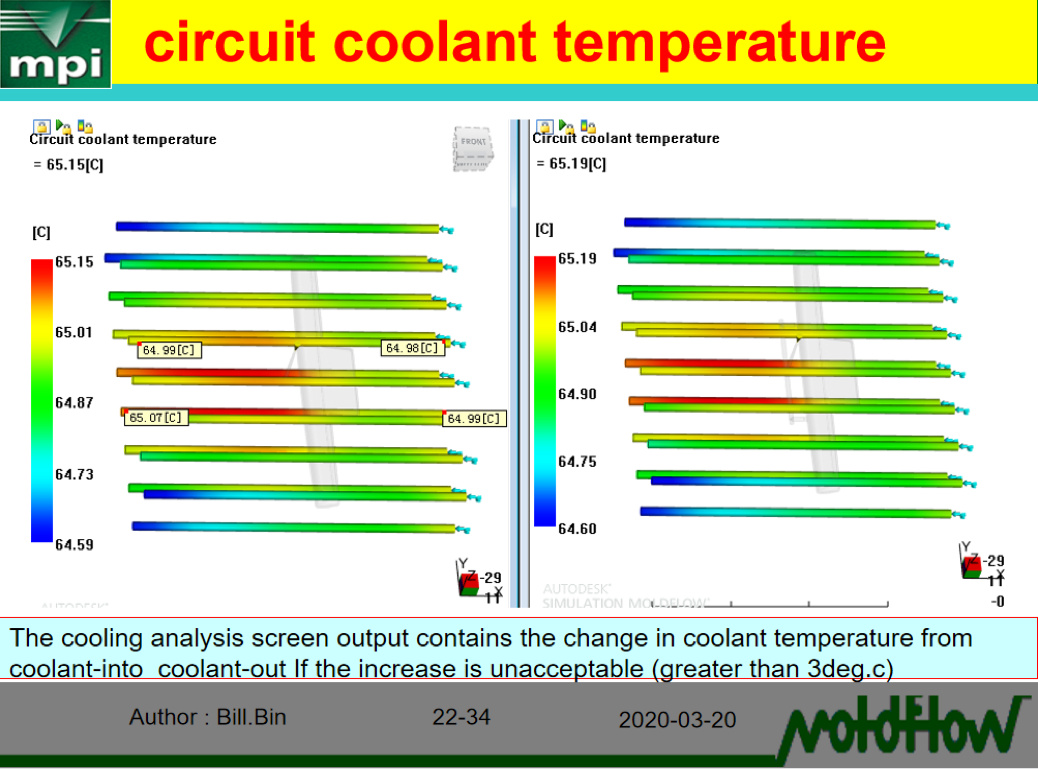
Mold flow
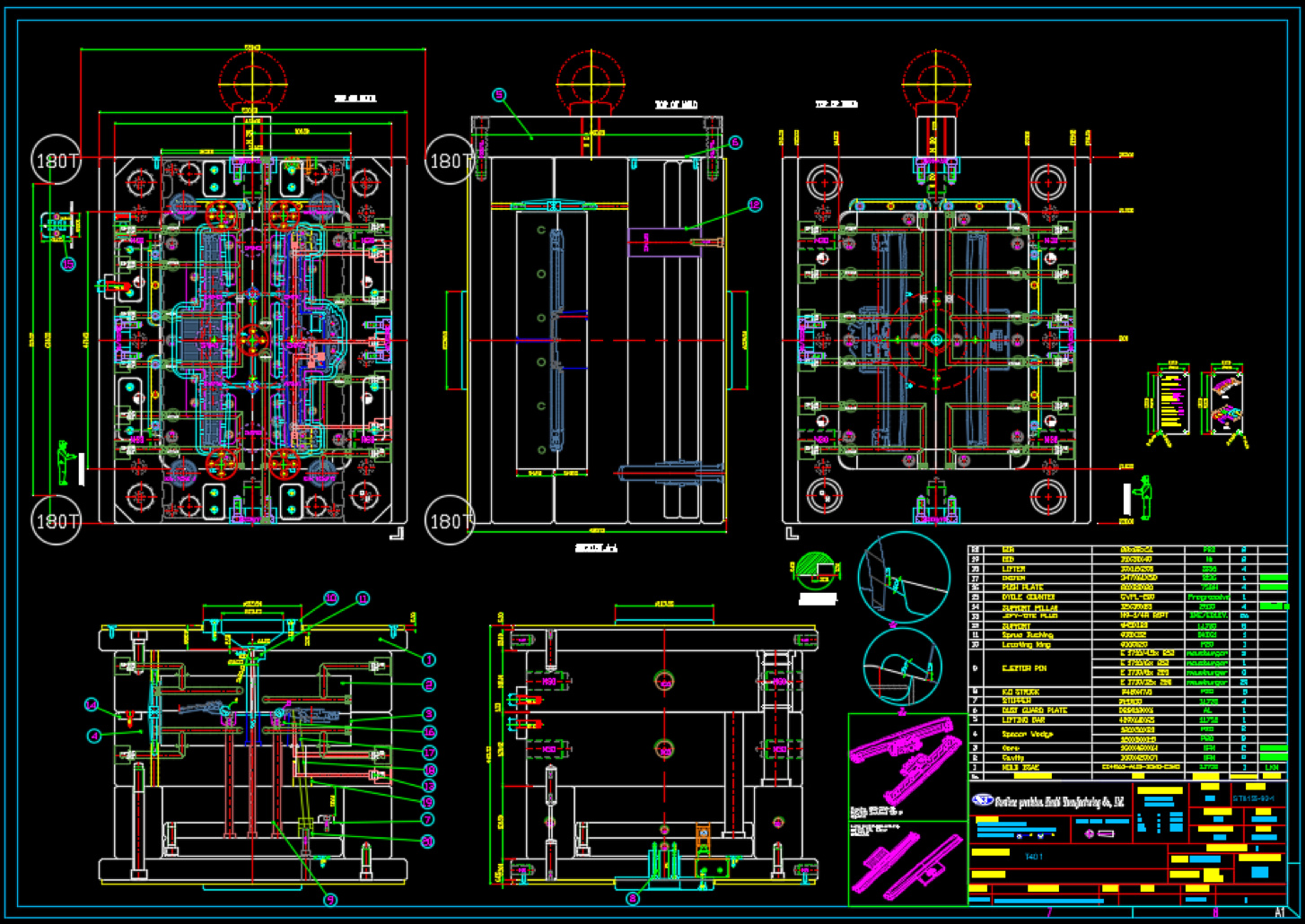
2D layout
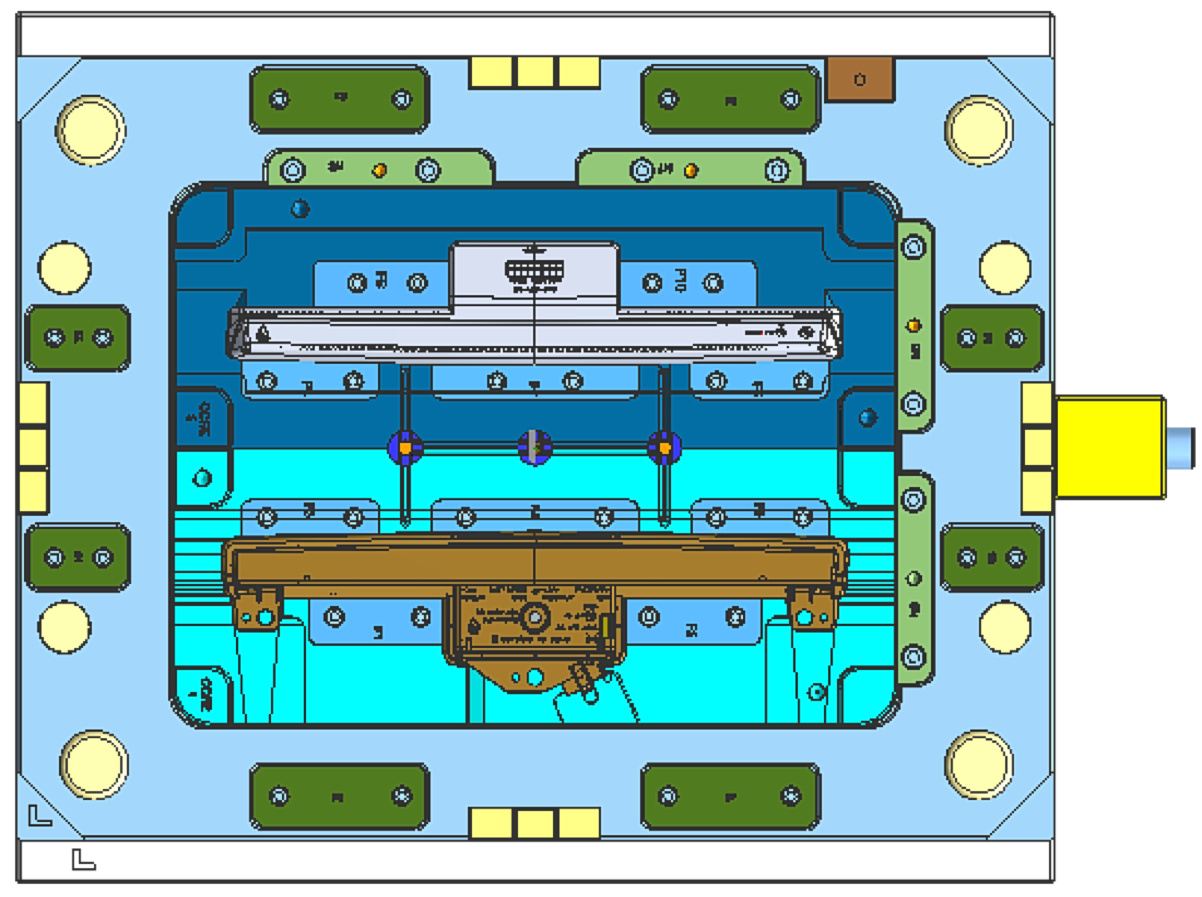
3D mold design
1. How can you show the manufacturing process to your customers?
Our engineers will communicate with customers directly and send weekly report every Monday with the time schedule and photos. If customers requires more information, we can provide photos, video or having video meeting with them.
2. What about your mold package for shipping?
After double check the mold before delivery, we will prepare a Memory stick with Final 2D&3D drawings, necessary Electrodes, Certification of steel and hard treatment, some replacement spare parts and other things that customers required together with mold.
We will use little protection oil on the mold and vacuum packing or Anti-rust paper depending on customer’s request. The box will be Customized Plywood box.