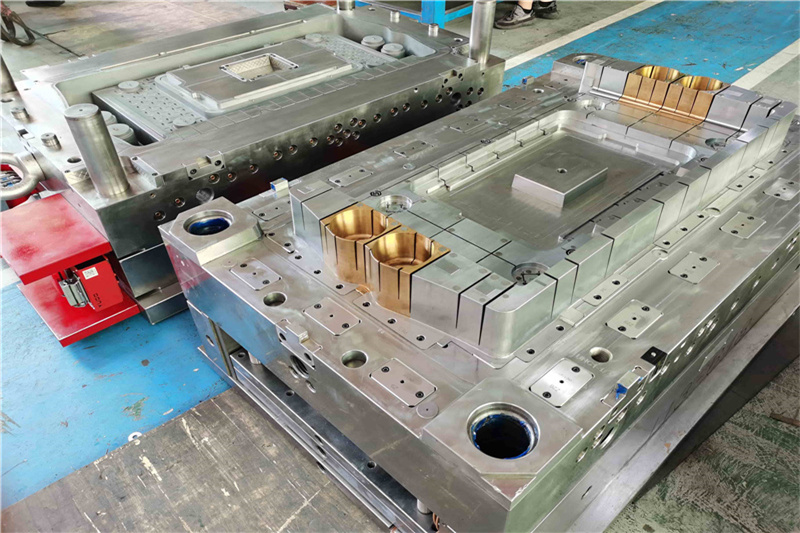
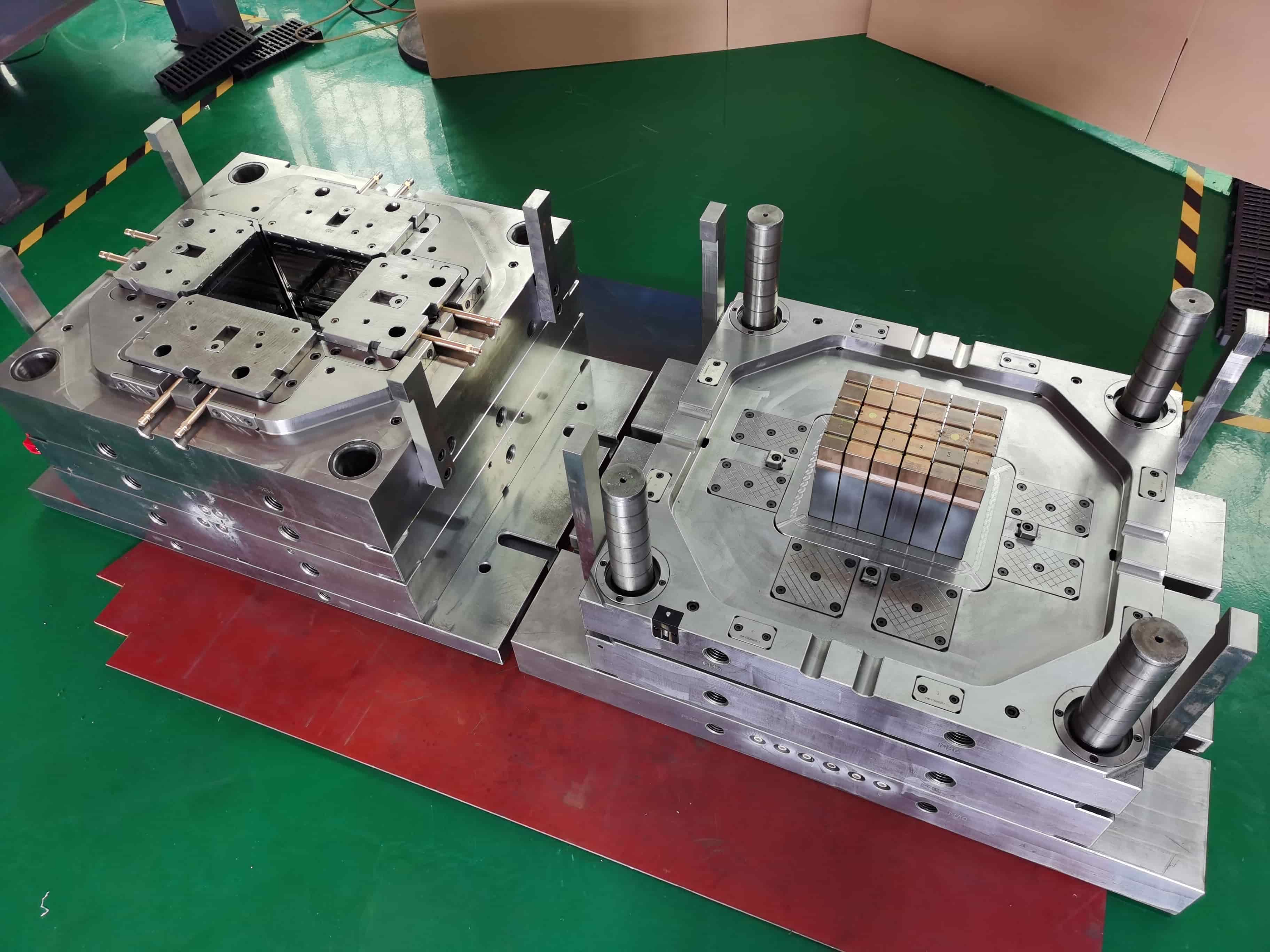
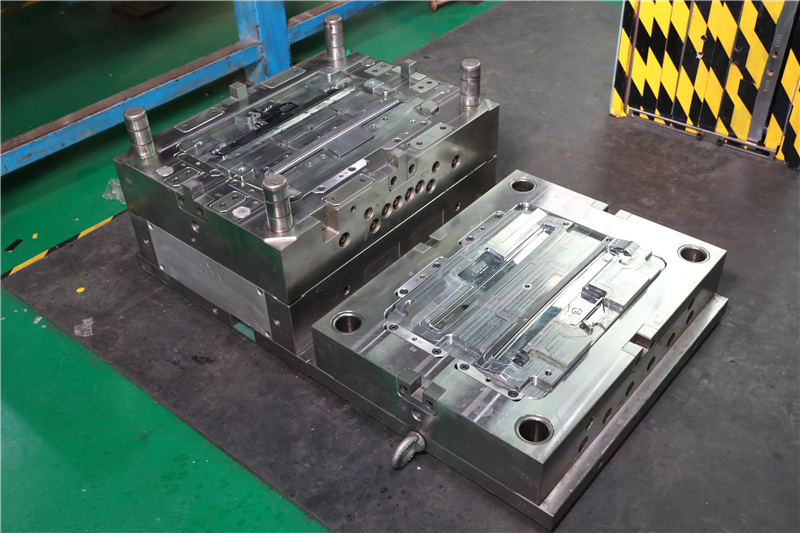
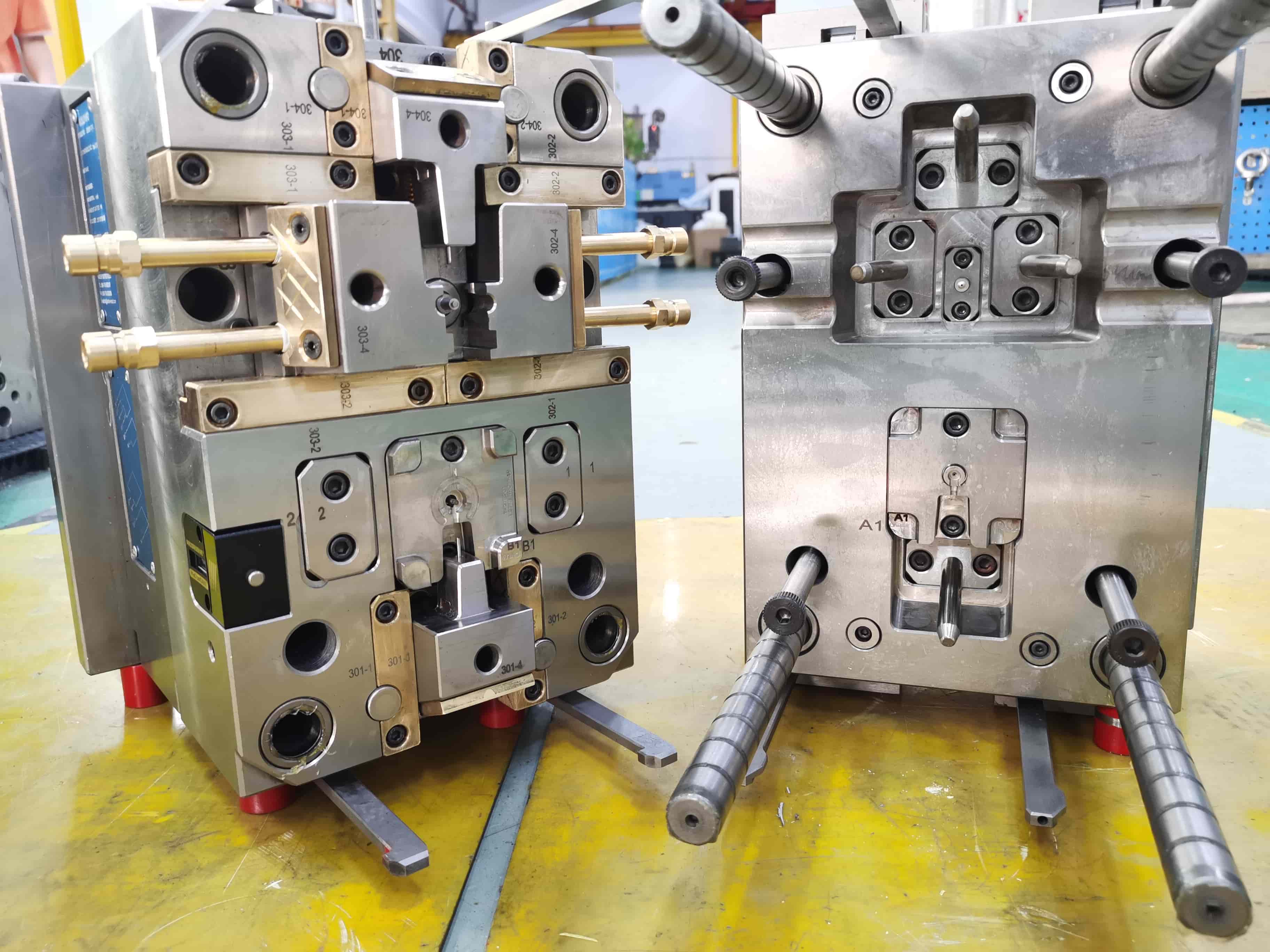
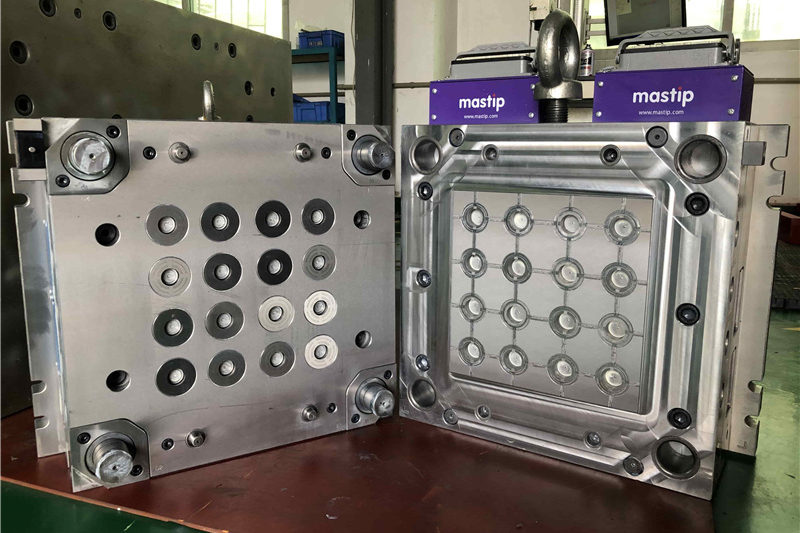
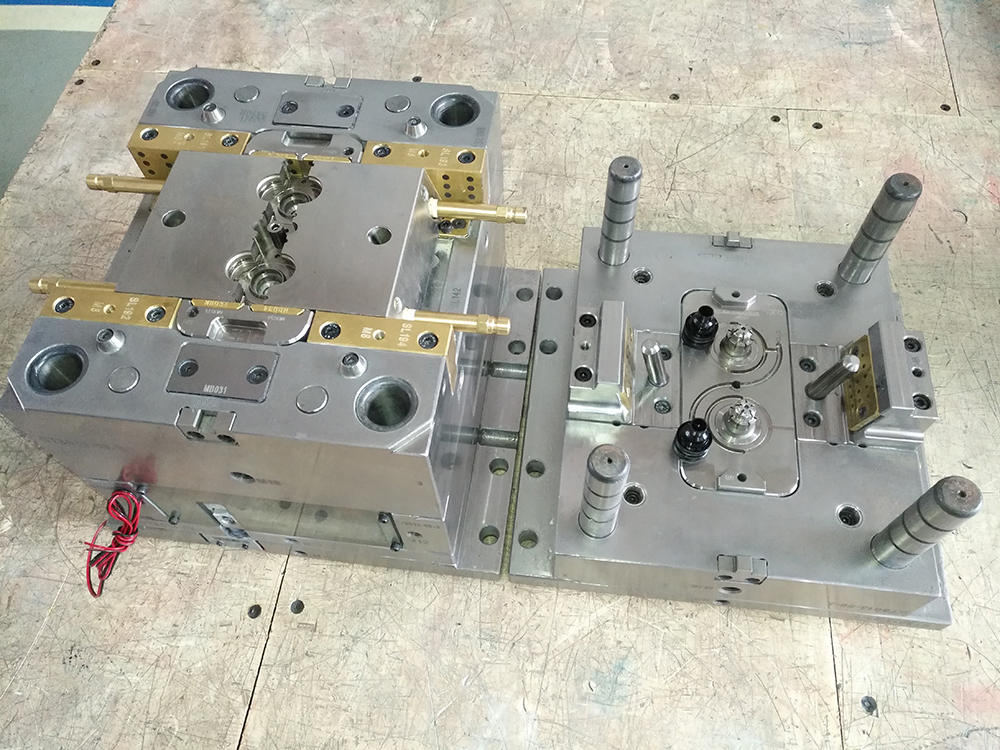
Things you want to know about injection mold
A good mold design is the critical start. With your part drawings (2d/3d), our designers and engineers will have a meeting to discuss the part structure, difficulties, customer's requests and have a concept of mould design for it.
1. DFM: show the mould layout concept, cooling, injection system, ejection system, wall thickness, draft angle, engraving, surface finishing, design failure mode and effects analysis and other mould release issues.
2. Mold flow (offer within 1~3 days)
3. Mould 2D layout design (offer within 2~4 days)
4. Mould 3D design (software: UG, offer within 2~5days)
What is a good mold? It must have good quality to meet production requests stable and smoothly, and no need to spend too much time & cost for maintenance and repair.
Suntime has 6 designers in total with more than 5-10 years’ experience, they always pay special attentions on customers' specification and details by thinking about the cost-saving solution based on stable and good quality. Their years’ experience for exporting molds give them great knowledge for global mold standards and quality demands.
A mold design reference for Automotive lighting cover

A plastic injection mold maker can help customers in a variety of ways. We can create custom plastic parts that meet their exact specifications and demands. We can offer design and engineering services to ensure that the final product meets the customer's exact needs. And we provide after service like maintenance and repairs for existing plastic injection molds to keep them running optimally no matter in our factory or in customers' company.
As an injection mould toolmaking, we can do for you as below:
1. Pre-sales support including but not limited in offering fast quotation, consultant of material options, tooling DFM analysis and so on.
2. Mold design from DFM, Mold flow, 2D layout design and 3D mold design. (within 2~4 working days)
3. Custom mold manufacturing for Plastic & Aluminum.
4. Engineering service for project following and other related work like outsourcing
5. Mold trials and low volume injection molding production before mold shipping
6. Mold modification / correction fastly
7. Transportation of shipping by air, sea or train.
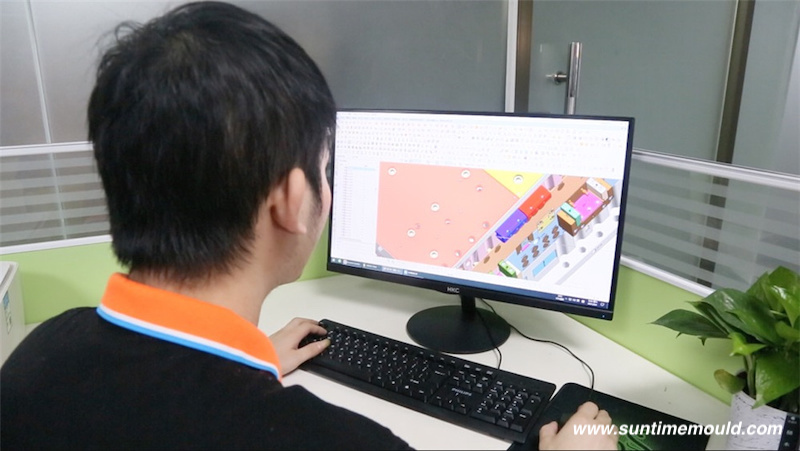
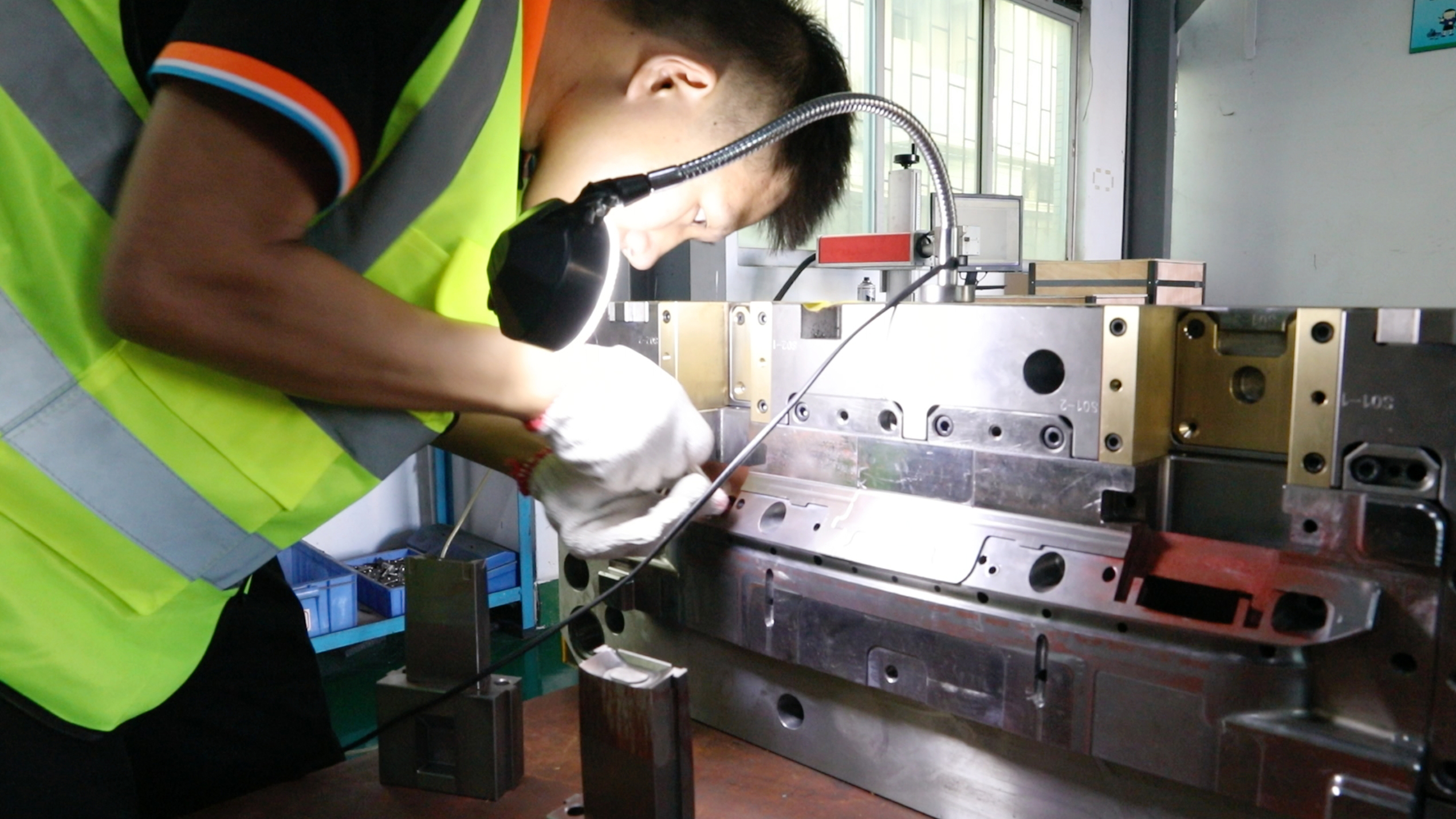
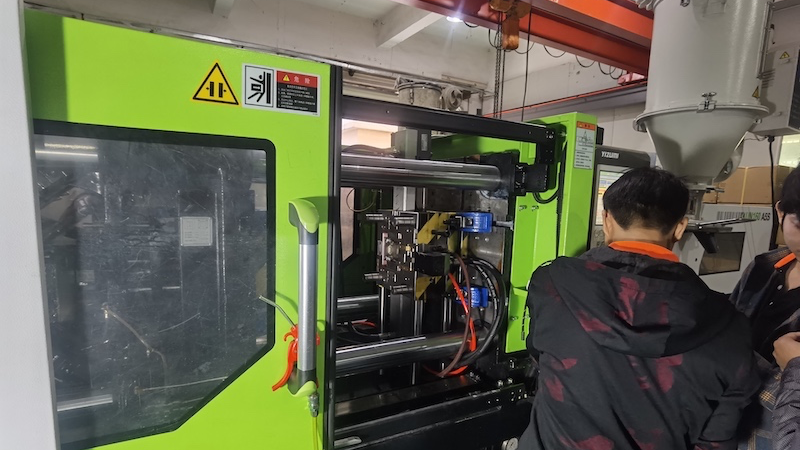
What we do for your project management (work flow)?
Step 1: With customers' parts drawing (2D&3D) and specification, we hold kick off meetings with designers, engineers and operation manager together to learn details and make memo for the projects.
Step 2: After customers approval for DFM, they start the 2D layout & 3D mold drawing & Mold flow analysis in short time.
Step 3: During all the process, weekly report will be provided every Monday to make sure customers have all things under control.
Step 4: For mold trials, we send trial report with mold photos, samples photos, short shot photo, weight photo, moulding issues and our solutions.
Meanwhile, Moulding video, inspection report and moulding parameter will be provided as fast as possible after.
Step 5: With customers’ approval to send samples, we send parts by express under Suntime's account.
Step 6: Mold corrections or modifications will be started at once after communication with customers.
Step 7: Mold can be shipped with customers' approval. More than 50% molds were required to ship after T1.
Step 8: Shipping package including: memory stick with final 2D&3D mould design, BOM, material certifications, photos and some spare parts.
Step 9: Clean molds and double check with QC checking list before packing.
Step 10: Vacuum packing for transportation.
Step 11: Documents and sales support for custom clearance.
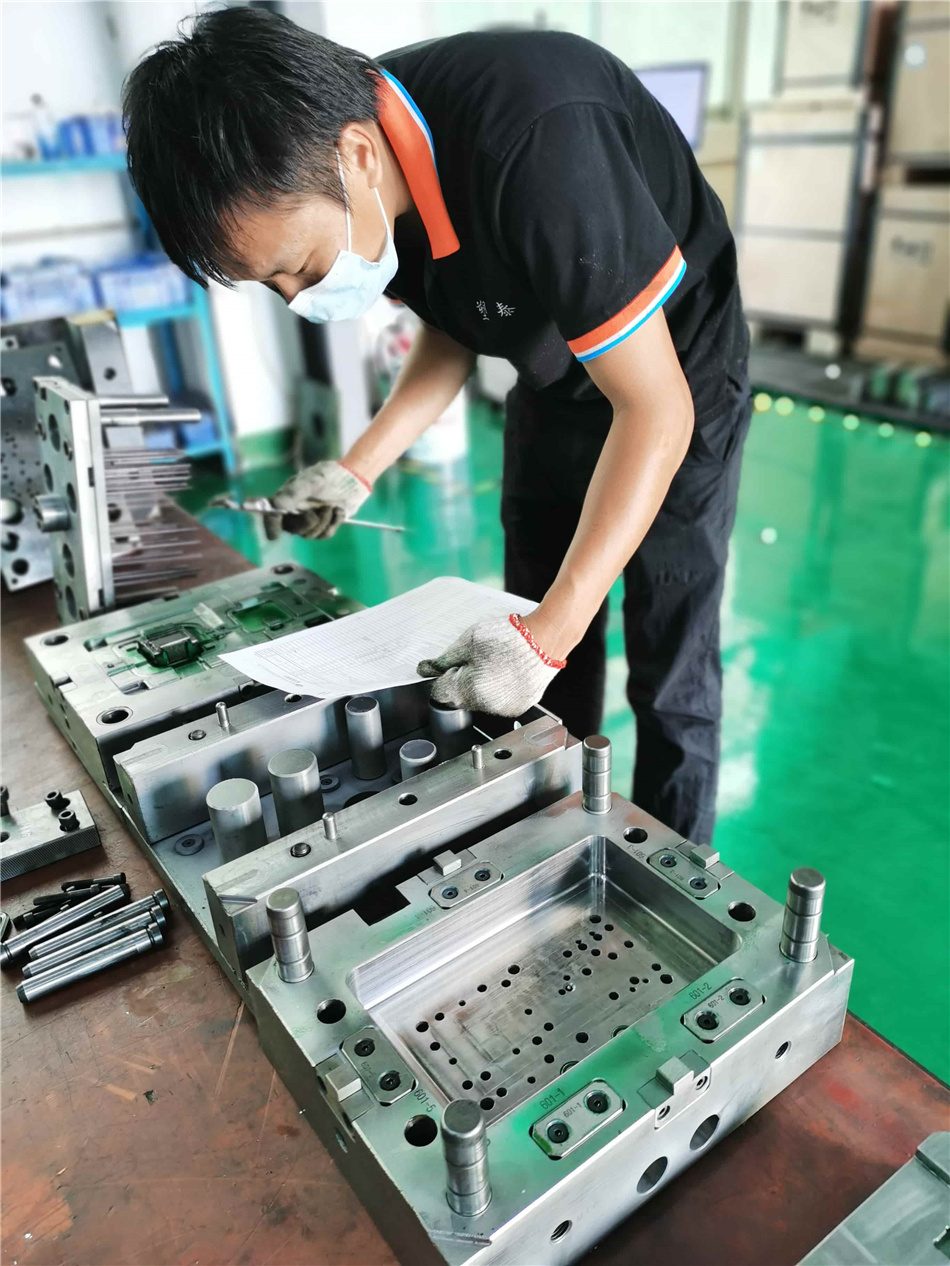
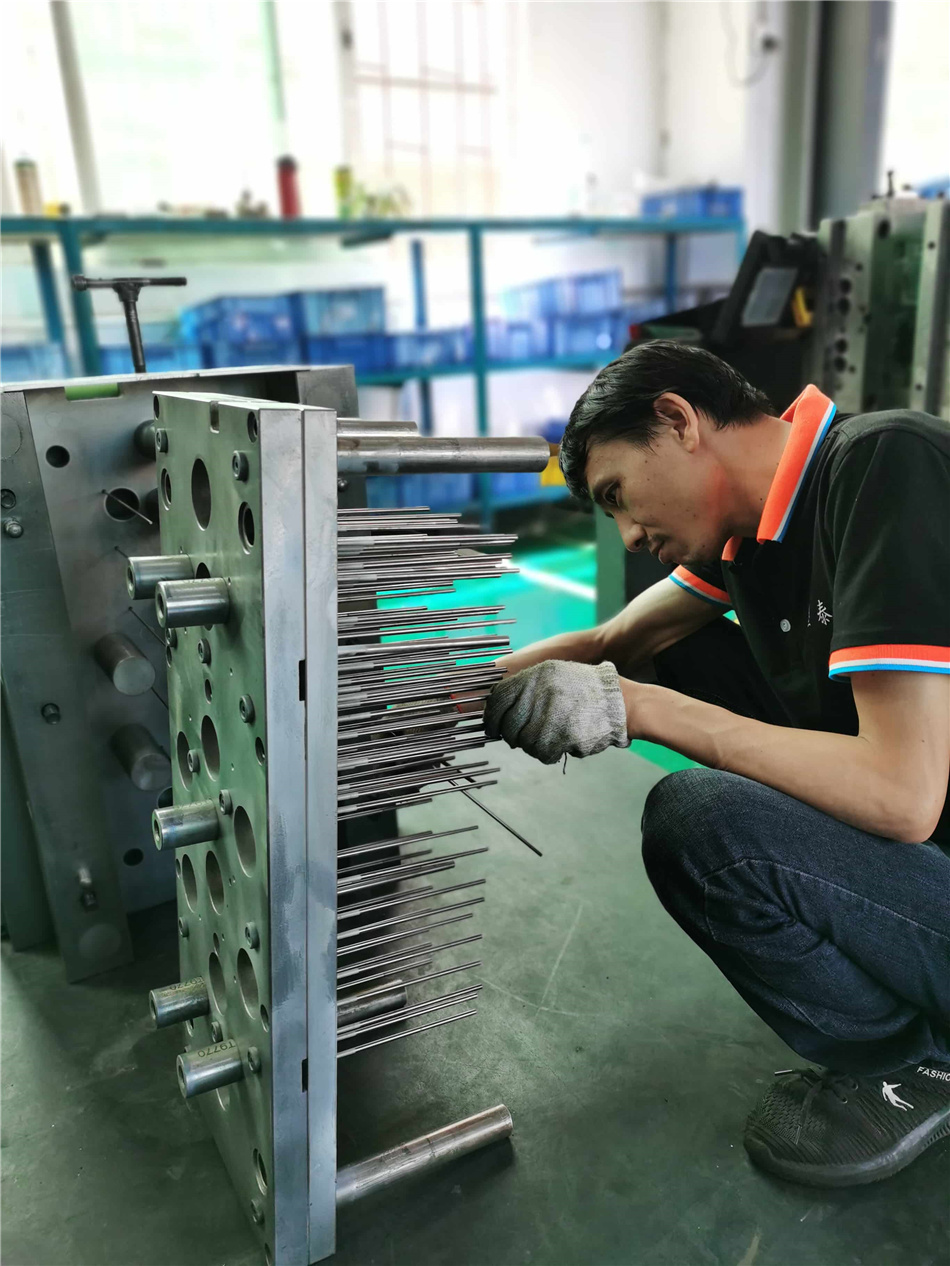
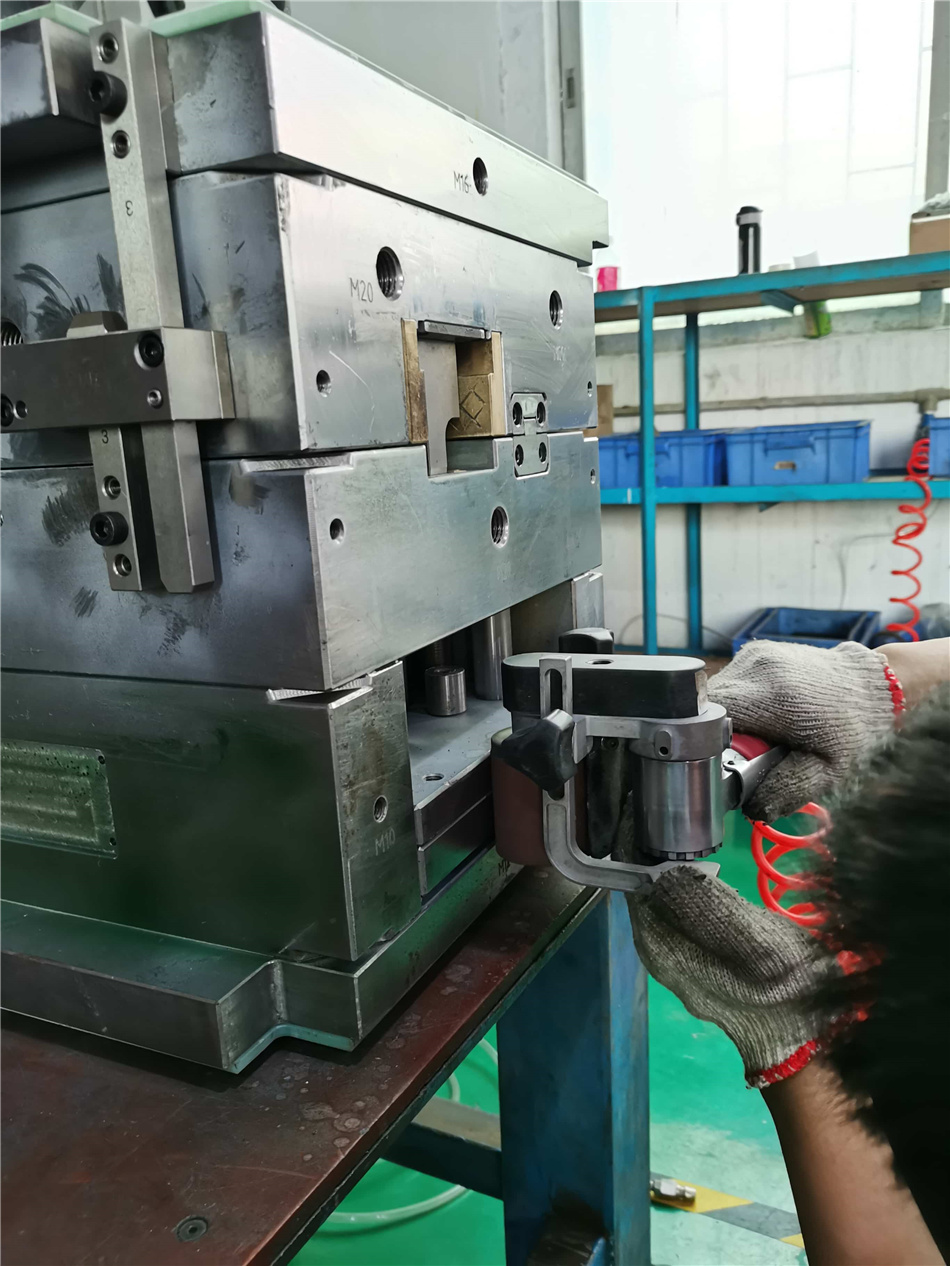
Quotation will be provided within 24 hours from SPM!
Please send us part 2D/3D drawings for a quick quotation.
If no drawings, clear photos showing the structure and dimension, or, samples to our factory directly.
File format: Dwg, Dxf, Edrw, Step, Igs, X_T
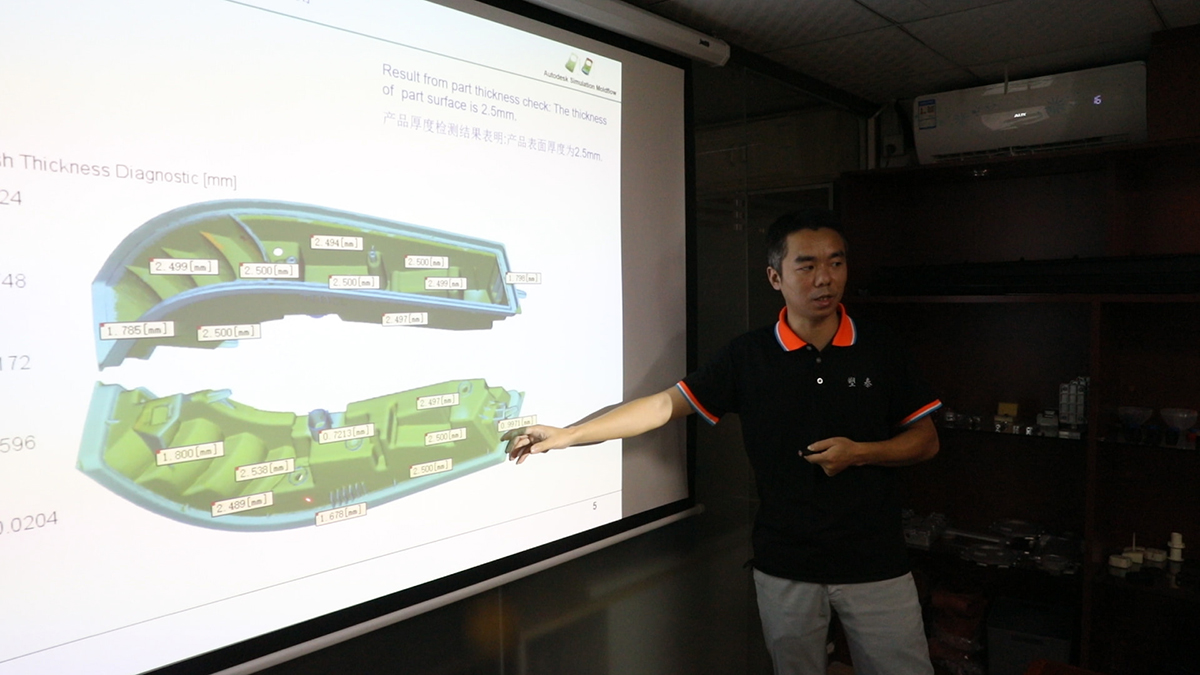
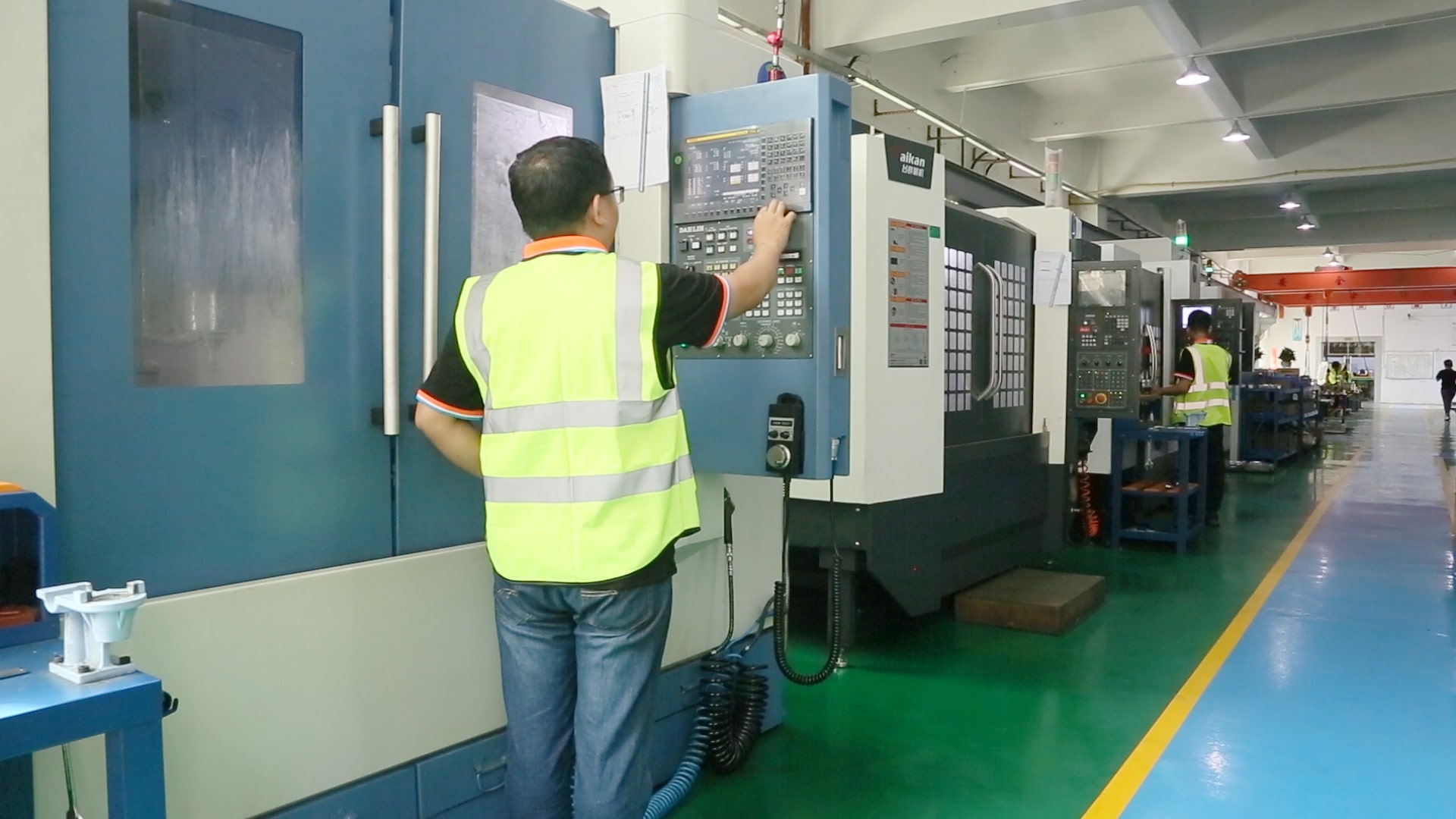
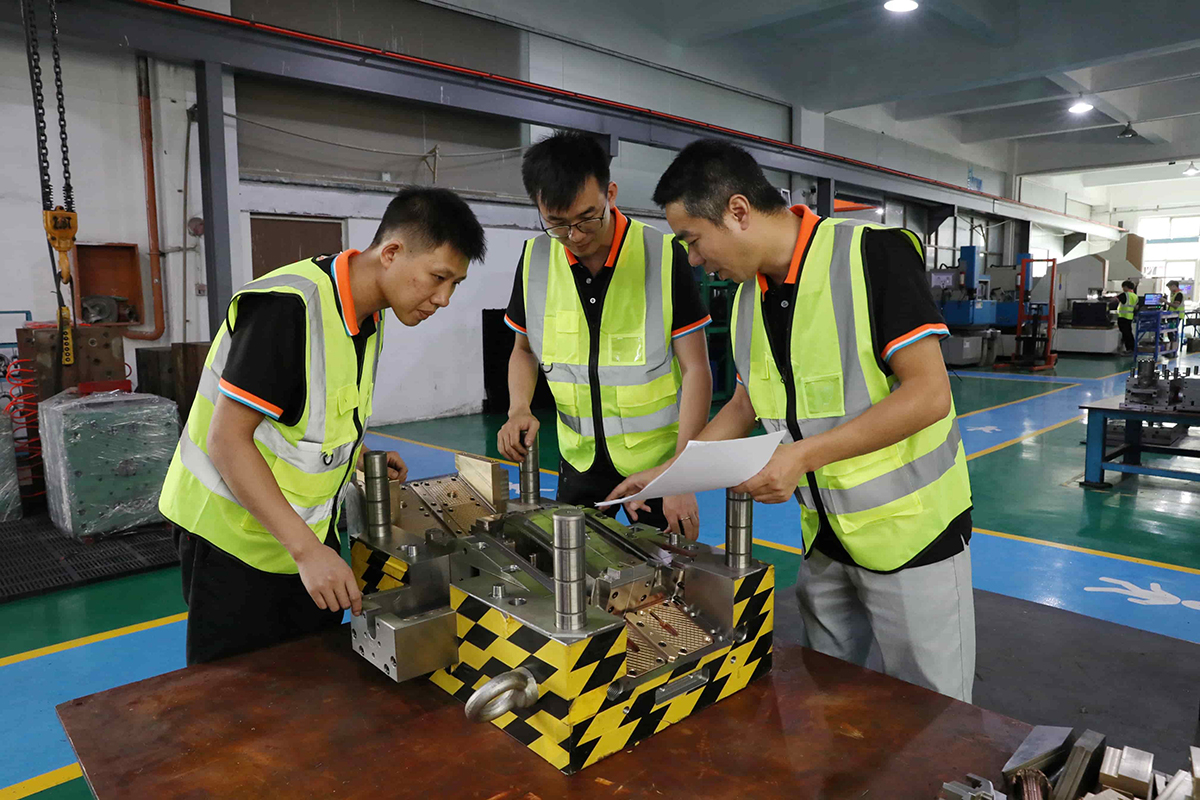
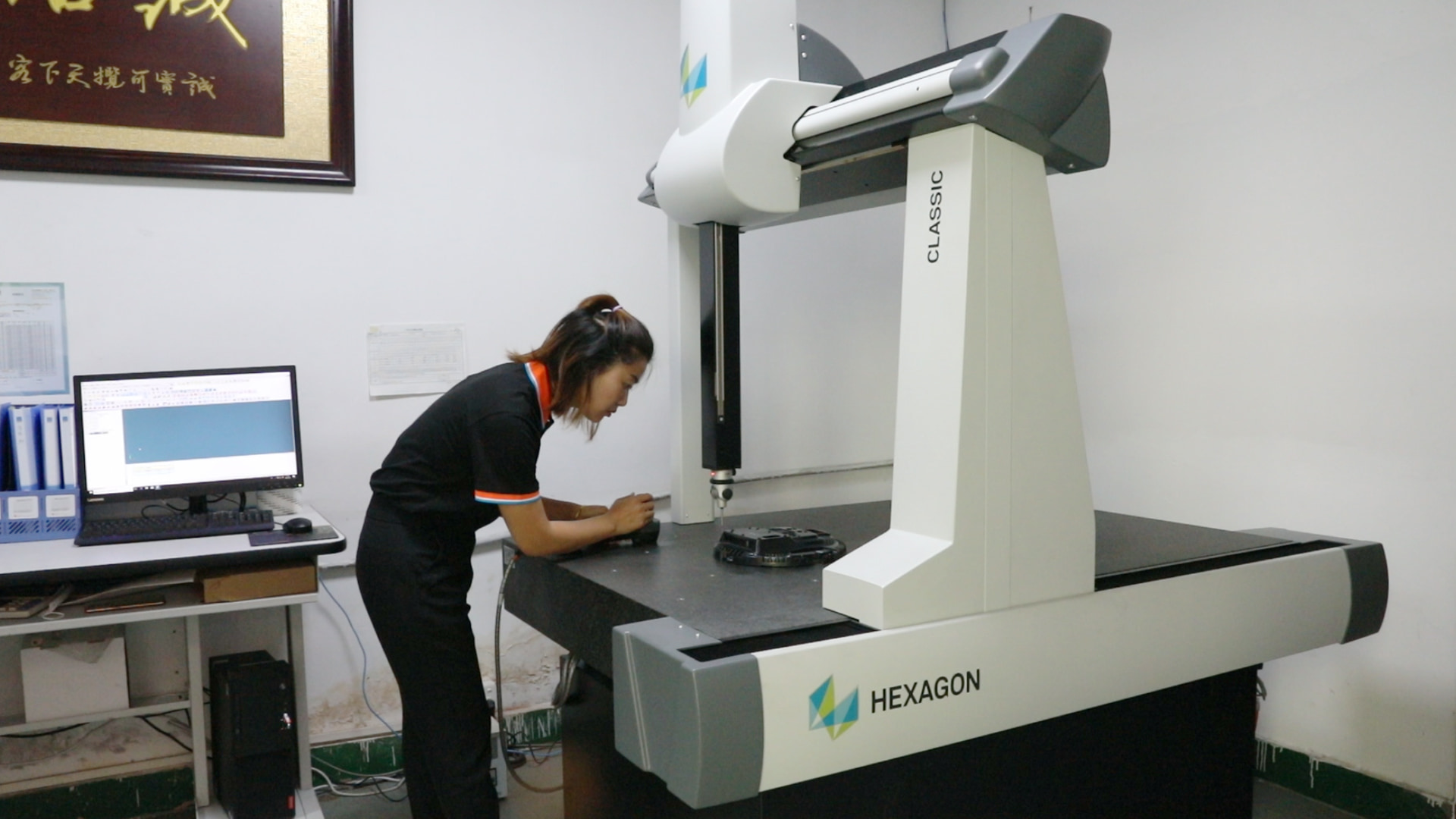
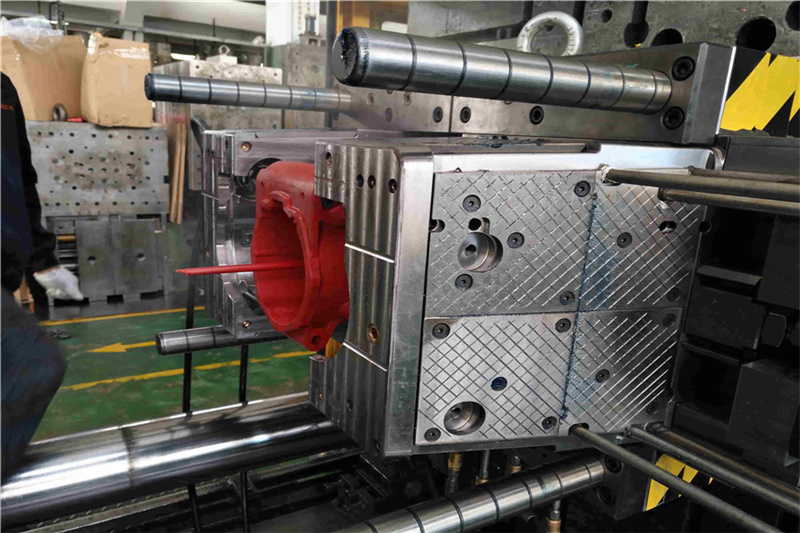
Process steps of manufacturing for an injection mold
The process of making a plastic injection mold can be broken down into the following steps:
Design: DFM analysis for mouldability. Create a 2D&3D mold drawings.
Machining: Cut steel and use machines like CNC, EDM, lathe and others to make the shape based on drawings.
Hardening: Heat treat the metal to make them reach to the hardness and more durable.
Surface: Polishing and textures to meet the cosmetic requests.
Assembly & Fitting: Put together all components of the final mold and do fitting.
Mold Testing: Test that everything is functioning properly after assembly.
Inspection: With molded parts, make inspection of molds and samples by CMM, projector, etc,.
Corrections/ modification: According to the samples, make corrections or modifications that customers required.
Ship molds after customers' approval.
How to save cost for making a injection mold?
How to save cost for mold making? Firstly, you should know the purpose of the mold. What are you going to use it for? What are the dimensions of the object you want to create? What is the annual volume? How many cavities do you need? And how accuracy you want? All of these factors will affect the cost of the mold.
• Simplify the design as much as possible. The more complex the part design is, the more expensive the mold will be. If you can simplify the design, you will save money.
• Use standard materials. The cost of an injection mold can be reduced by using standard materials instead of exotic materials.
• Use a simple geometry. The simpler the geometry, the less expensive the mold will be.
• Minimize the number of parting lines. Parting lines are where two halves of the mold meet. The more parting lines there are, the more expensive the mold will be.
• Minimize the number of cores and inserts. Cores and inserts are pieces that are used to create cavities in the mold. The more cores and inserts there are, the more expensive the mold will be.
• Use a conventional manufacturing process. The cost of an injection mold can be reduced by using a conventional manufacturing process instead of a custom process.
• Use a simple gate design. The gate is where material enters the cavity of the mold during injection molded manufacturing . A simple gate design will reduce both material waste and cycle time, which will save money.
If you have a part on hand needing to make an injection mold, but not sure how to save cost as much as possible, contact us, we will provide a DFM analysis for free and let you know our ideas.










FAQ
Custom plastic injection mold manufacturing
Aluminum die casting mold
Normal plastic injection mold
Multi-cavity injection mold
Family moulds
Hot runner systems mold
MUD mold
Over mold
2K mould
Thin Wall mold
Rapid prototyping mold
Mold Flow: Mould FlowAnalysis
3D Modeling: Unigraphics, Pro/Engineer, Solidworks (files: step,Igs,X-T,prt,sldprt.)
2D Drawing: Auto-CAD, E-drawing (files: dwg,dxf,edrw)
Steel Brand: GROEDITZ/ LKM/ ASSAB/ DAIDO/ FINKL...
Mould Base: LKM,DME,HASCO,STEIHL....
StandardComponents: DME, HASCO, LKM, Meusburger….
Hot Runner: Mold master, Mastertip, Masterflow, Husky, Hasco, DME, Yudo, Incoe, Syventive, Mold master…
Polishing/Texture: SPI,VDI, Mold-Tech, YS....Molding
PEEK, PPSU,ABS, PC, PC+ABS, PMMA, PP, HIPS, PE(HDPE,MDPE,LDPE). PA12, PA66, PA66+GF,TPE,TPR,TPU, PPSU, LCP, POM, PVDF, PET, PBT, etc,.
A380, AL6061, AL5052, etc, .
DFM/Mold flow: 1~3 working days
2D design: 2~4 working days
3D design: 3~5 working days
Quotation within 24 hours!
You can contact us by Emails, phone calls, video meetings, or require visiting
Engineers contact directly in English
The lead time of mould manufacturing (from design approval to T1) is 3~8 weeks depends on mold complexity and structure.
But for normal projects, it is 4~5 weeks.
Yes, we are ISO9001:2015 certificated
Yes, we have 7 injection molding machines.
Our main customers are located in North America (USA, Canada), Europe (Germany, UK, Norway, Denmark, Portugal and so on ) and Australia