The 5 Points of Knowledge of Injection Molds
Introduction
Injection molds are crucial tools in the manufacturing of plastic parts. They enable the mass production of intricate and high-quality plastic components. This article aims to provide comprehensive knowledge about injection molds from 5 points of mold types, standards, mold steel selection, hot runner systems, and surface requirements. Understanding these key elements is essential for designers, engineers, and manufacturers involved in the plastic injection molding industry.
Types of Injection Molds
Injection molds come in various types, each designed for specific applications, below are 4 types of injection molds for your reference.
1. Two-Plate Mold: This is the most basic type of mold, consisting of two plates that separate to eject the molded part.
2. Three-Plate Mold: This type of mold includes an additional plate called the runner plate. It allows for the separation of the sprue and runner system from the part, facilitating easier ejection, the gate will be pin point gate.
3. Hot Runner Mold: In this mold type, the plastic material is kept molten within the mold runner system, eliminating the need for a sprue and runner separation. It enables faster cycle times and reduced material waste. There are many famous hot runner brands such as Mold master, master flow, Syventive, Yudo, Incoe and so on.
4. Family Mold: A family mold allows multiple parts to be molded simultaneously, typically with different cavities and configurations. This type of mold is cost-saving and it can be designed with runner shut-off so that no waste happens when only one can part is needed.

Mold Standards
Mold standards play a crucial role in ensuring injection molds' quality, performance, and longevity. Two key factors considered when defining mold standards are mold life and steel requirements like the US SPI-SPE mold standard.
Mold Life: Mold life refers to the number of cycles a mold can produce before its performance degrades. Mold life requirements vary based on the specific application and production volume. Common mold life standards include low-volume molds (up to 100,000 cycles), medium-volume molds (100,000 to 500,000 cycles), and high-volume molds (over 500,000 cycles).
Steel Requirements: The choice of mold steel is crucial for mold performance and longevity. Mold steel should have excellent wear resistance, high hardness, good thermal conductivity, and sufficient toughness. Common mold steel standards include P20, H13, S136, and 718, with each offering specific properties suitable for different molding applications.
As a mold maker with over 10 years of experience for exporting, sometimes we refer to mold standard based on mold components brands such as DME, HASCO, LKM and so on.
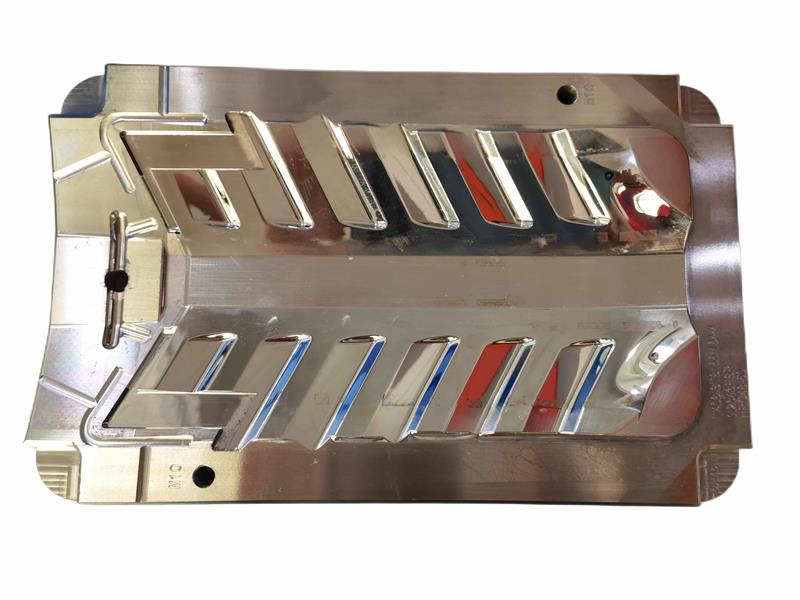
Types of Mold Steel
P20: P20 is a versatile mold steel with good toughness and wear resistance. It is commonly used for low to medium-volume production molds.
H13: H13 is a hot-work tool steel known for its high hardness and excellent heat resistance. It is suitable for molds subjected to high temperatures and high production volumes.
S136: S136, also known as stainless steel, offers excellent corrosion resistance and good polishability. It is commonly used for molds requiring high surface finishes.
718: 718 is a pre-hardened mold steel with good polish ability and machinability. It offers a balance of toughness, wear resistance, and surface finish capabilities.
There are many different types of mold steel and brands, the use of them depends on the requests of mold life and plastic material. Normally the mold base is soft steel, but mold core insert plates are requested to be hardened steel which means the steel needs to be heat treated and reach enough HRC.
Types of Hot Runner Systems
When we design a plastic injection mold, we will choose a cold runner or hot runner based on the complexity of the part, cost aspect, and others. Our engineer will give suggestions to customers when we have better solutions, but we do as customers request finally.
Here let’s talk about the Hot runner systems. Common types of hot runner systems include:
Valve Gate Hot Runners: Valve gate systems precisely control the flow of molten plastic using individual valve pins. They offer excellent gate quality and are suitable for high-precision molding.
Open Gate Hot Runners: Open gate systems have a simpler design and are cost-effective for applications that do not require highly controlled gating.
Hot Sprue Bushing: Hot sprue systems use a heated sprue bushing to transfer molten plastic from the injection unit to the mold cavities. They are commonly used in molds with single or multiple cavities.

Mold Surface Requirements
Mold surface requirements depend on the specific part design, aesthetics, and functional needs. According to our experience, there are normally 4 surface types for injection molds.
High Gloss Finish: A high-gloss surface finish is achieved through meticulous polishing and surface treatment processes. It is desirable for parts with a premium appearance.
Textured Finish: Textured finishes can be applied to mold surfaces to create specific patterns or textures on the molded part. This enhances grip, hides surface imperfections, or adds visual interest.
Matte Finish: Matte finishes provide a non-reflective surface and are often used for functional parts or components that require minimal glare.
Grain Finish: Grain finishes replicate natural materials such as wood or leather, adding a tactile and aesthetic quality to the molded part.
Conclusion
Injection molds are essential tools in the plastic injection molding industry. Understanding the different mold types, mold standards, types of mold steel, Runner systems, and surface requirements is crucial for achieving highly efficient production. By considering these aspects, designers, engineers, and manufacturers can select the appropriate mold type, steel, runner system, and surface finish to make their projects successful.
Post time: Jun-28-2023