What is the difference between plastic injection molding and die casting?
Injection-molded products are parts made of plastics by using injection molding machines and molds to be shaped products, while die-cast products are parts made of metal through injection machines and die-casting molds, they are very similar in tooling, molding machines and production processes. Today let’s take a look at the differences between injection molding and die casting in the below 10 points.
1. Materials: Plastic injection molding typically uses lower-temperature materials such as thermoplastics, while die casting often requires higher-temperature materials such as metals.
Materials Used in Plastic Injection Molding:
Thermoplastics
Acrylonitrile Butadiene Styrene (ABS)
Polycarbonate (PC)
Polyethylene (PE)
Polypropylene (PP)
Nylon/Polyamide
Acrylics
Urethanes
Vinyls
TPEs & TPVs
......
Materials Used in Die Casting:
Aluminum Alloys
Zinc Alloys
Magnesium Alloys
Copper Alloys
Lead Alloys
Tin Alloys
Steel Alloy
......
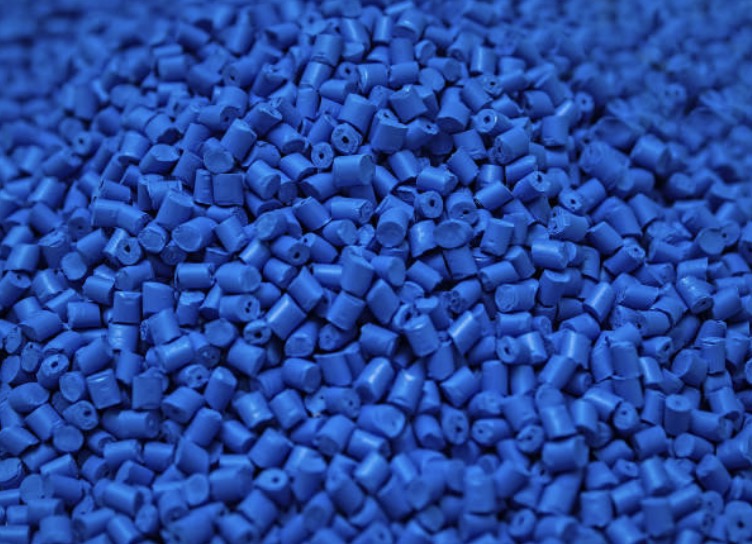
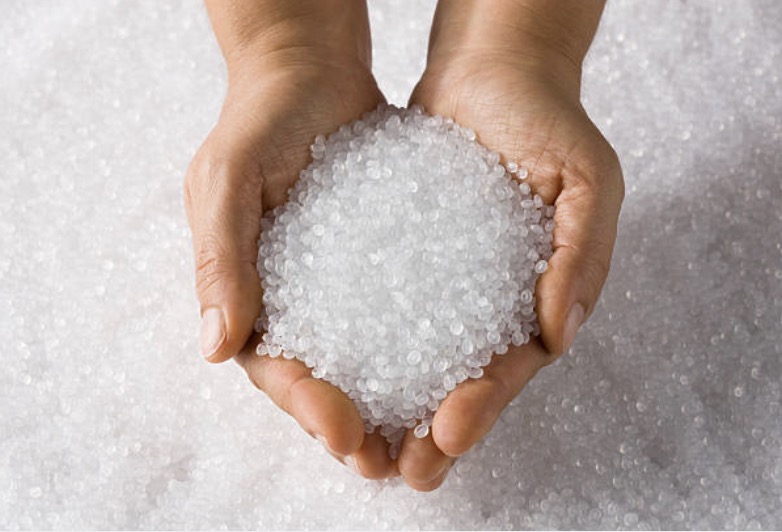
2. Cost: Die casting is generally more expensive than plastic injection molding since it requires higher temperatures and specialized equipment.
Costs associated with die casting a part typically include:
• The cost of the raw materials used in the process, such as alloys and lubricants.
• The cost of the machinery used for die casting (injection molding machines, CNC machining, Drilling, tapping, and so on).
• Any costs associated with maintaining and repairing machinery and tools.
• Labor costs such as those related to setting up, running and inspecting the process and the risk of danger as the metal would be very high temperature.
• Secondary operations such as post processing or finishing treatments that may be necessary for some parts. Compared with plastic parts, there will be more secondary machining cost and surface cost like anodizing, plating and coating, etc,.
• Shipping costs to send the finished parts to their destination. (The parts will be much heavier than plastic parts, so the shipping cost would be high too. Sea shipping can be a good choice, but only need to do the plan earlier as sea shipping needs much more time.)
Costs associated with plastic injection molding a part typically include:
• The cost of the raw materials used in the process, including resin and additives.
• The cost of the machinery used for plastic injection molding. (Normally, plastic parts can have complete good structure after molding, so there will less cost for secondary machining.)
• Any costs associated with maintaining and repairing machinery and tools.
• Labor costs such as those related to setting up, running and inspecting the process.
• Secondary operations such as post processing or finishing treatments that may be necessary for some parts. (plating, coating or silk-screen)
• Shipping costs to send the finished parts to their destination. (Plastic is not as heavy as mental, sometimes for urgent demand, they can be shipping by air and the cost will be lower than metal parts.)
3. Turnaround Time: Plastic injection molding usually has a faster turnaround time than die casting due to its simpler process. Normally, injection molded products don’t need secondary machining while most of die casting parts have to do CNC machining, drilling, and tapping before surface finishing.
4. Accuracy: Due to the high temperatures required for die casting, parts tend to be less accurate than those created with plastic injection molding due to shrinkage and warping and other factors.
5. Strength: Die castings are stronger and more durable than those produced using plastic injection molding techniques.
6. Design Complexity: Plastic injection molding is well suited for parts with complex shapes, while die casting is better for producing parts that are symmetrical or have fewer details molded into them.
7. Finishes & Coloring: Injection molded parts can have a wider range of finishes and colors compared to die castings. The main difference between the finishing treatments of injection molded parts and die castings parts is the material used. Die castings are typically made with metals that require further machining or polishing processes in order to achieve a desired finish. Plastic injection molded parts, on the other hand, are typically finished using thermal treatments and chemical coatings, which often result in smoother surfaces than those achieved through machining or polishing processes.
8. Batch Size & Quantities Produced: Different methods create different maximum batch sizes of parts; plastic injection molds can produce up to millions of identical pieces at once, whereas die casts can produce up to thousands of similar pieces in one run depending on their complex levels/formats and/or tool setup times involved between batches (i.e., changeover times).
9. Tool Life Cycle: Die cast tools require more cleaning and maintenance since they need to be able to withstand high heat temperatures; on the other hand, plastic injection molds have a longer life cycle due to its lower heat requirements during production runs which can help to offset costs associated with tooling/setup time/etc.
10 .Environmental Impact: Due to their cooler manufacturing temperatures, plastic injection molded items often have low environmental impact when compared with die casts like zinc alloy parts which require higher-heat temperatures in order for parts fabrication processes,
Writer: Selena Wong
Updated: 2023-03-28
Post time: Mar-28-2023