The history of plastic injection molding dates back to the late 1800s, although the technology has evolved greatly over the past century. It was first used as a means to mass produce rabbit and duck decoys for hunters in 1890. Throughout the 20th century, plastic injection molding became increasingly popular due to its accuracy and cost effectiveness for manufacturing products such as auto parts, medical devices, toys, kitchenware, sports equipment and household appliances. Today, it is one of the most commonly used manufacturing processes around the world.

Plastic injection molding is an incredibly versatile manufacturing process that has a wide range of applications, including:
• Automotive: Interior parts, Lightings, Dashboards, door panels, instrument panel covers, and more.
• Electrical: Connectors, Enclosures, Battery box, Sockets, Plugs for electronic devices and more.
• Medical: Medical devices, lab equipment, and other components.
• Consumer Goods: Kitchenware, Houseware, Toys, toothbrush handles, garden tools, and more.
• Others: Building products, Mining products, Pipes & fittings, Package and container, and more.
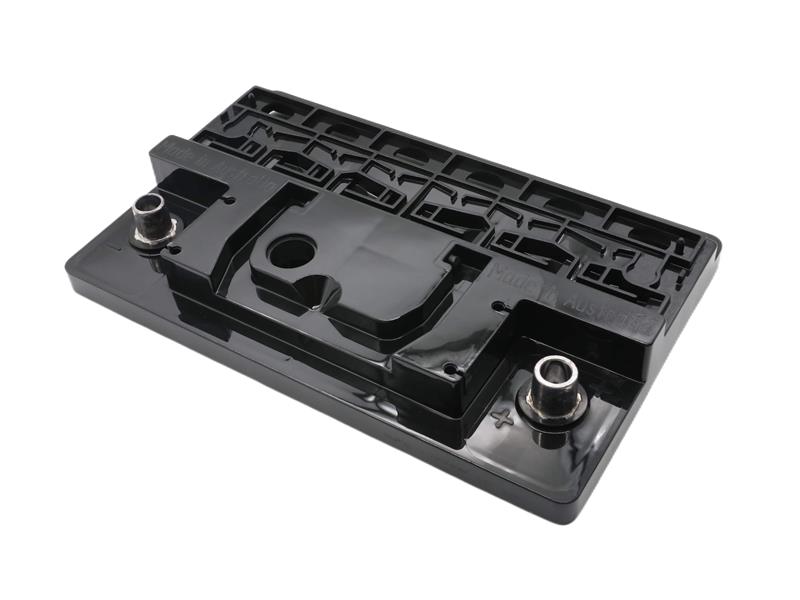
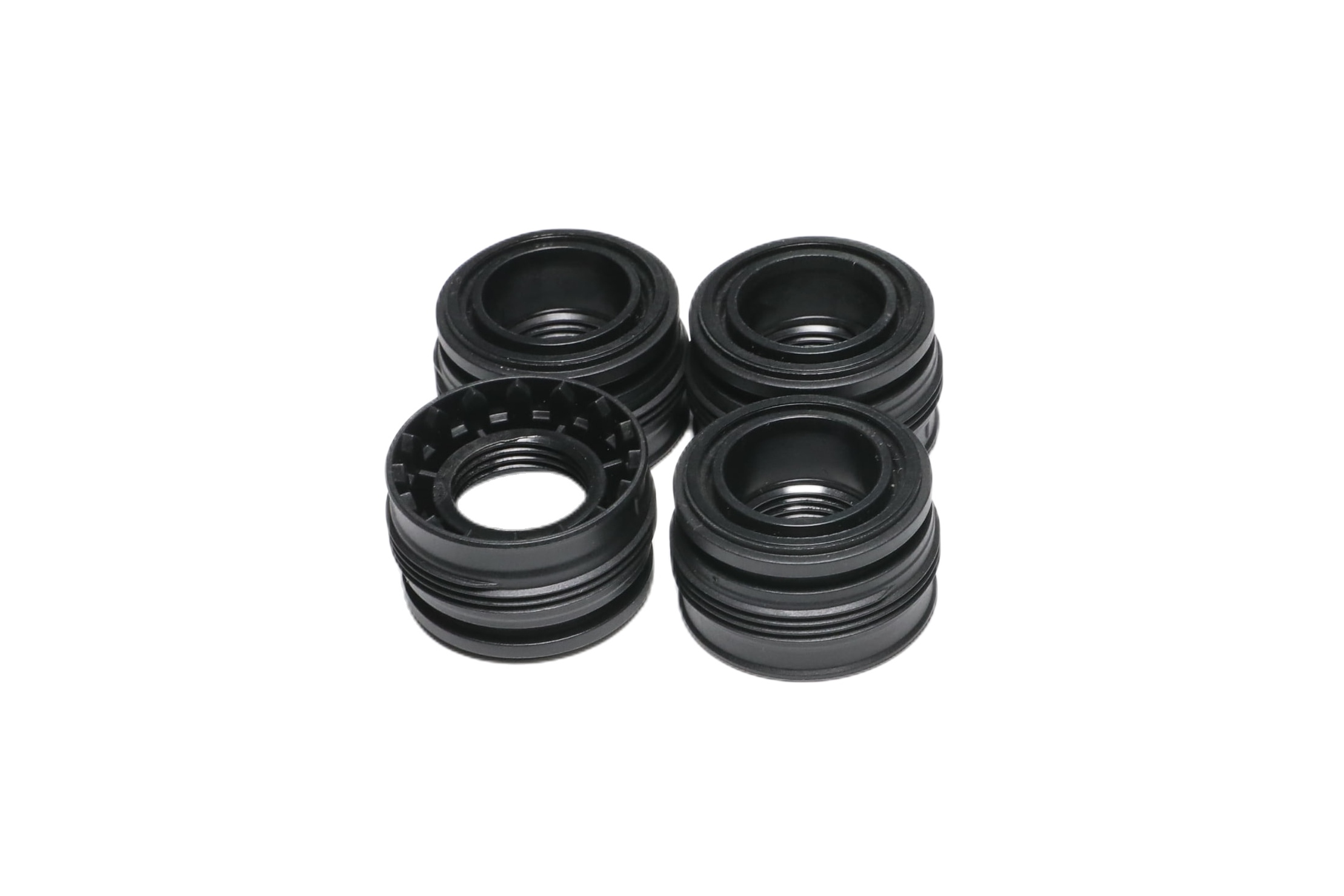
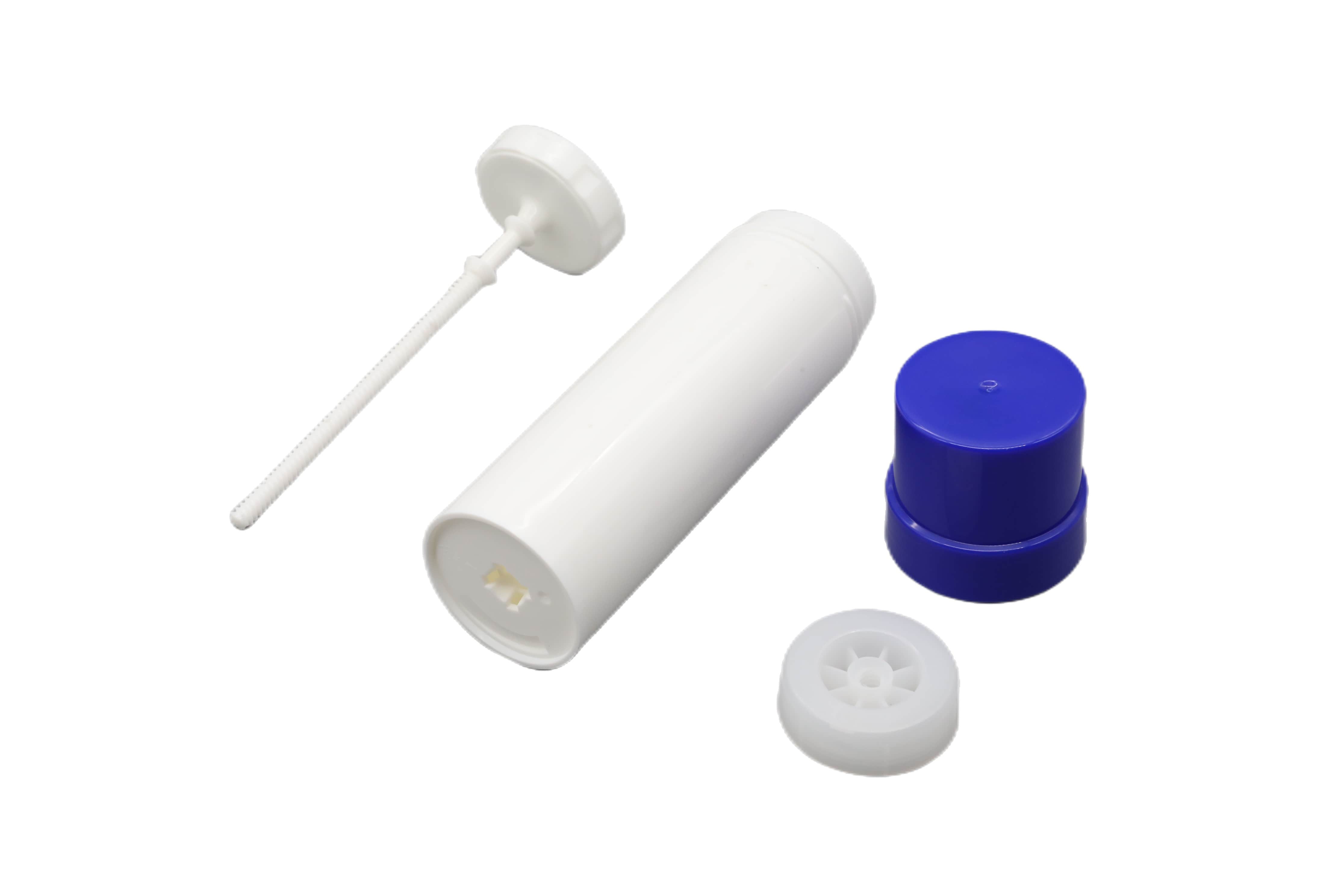
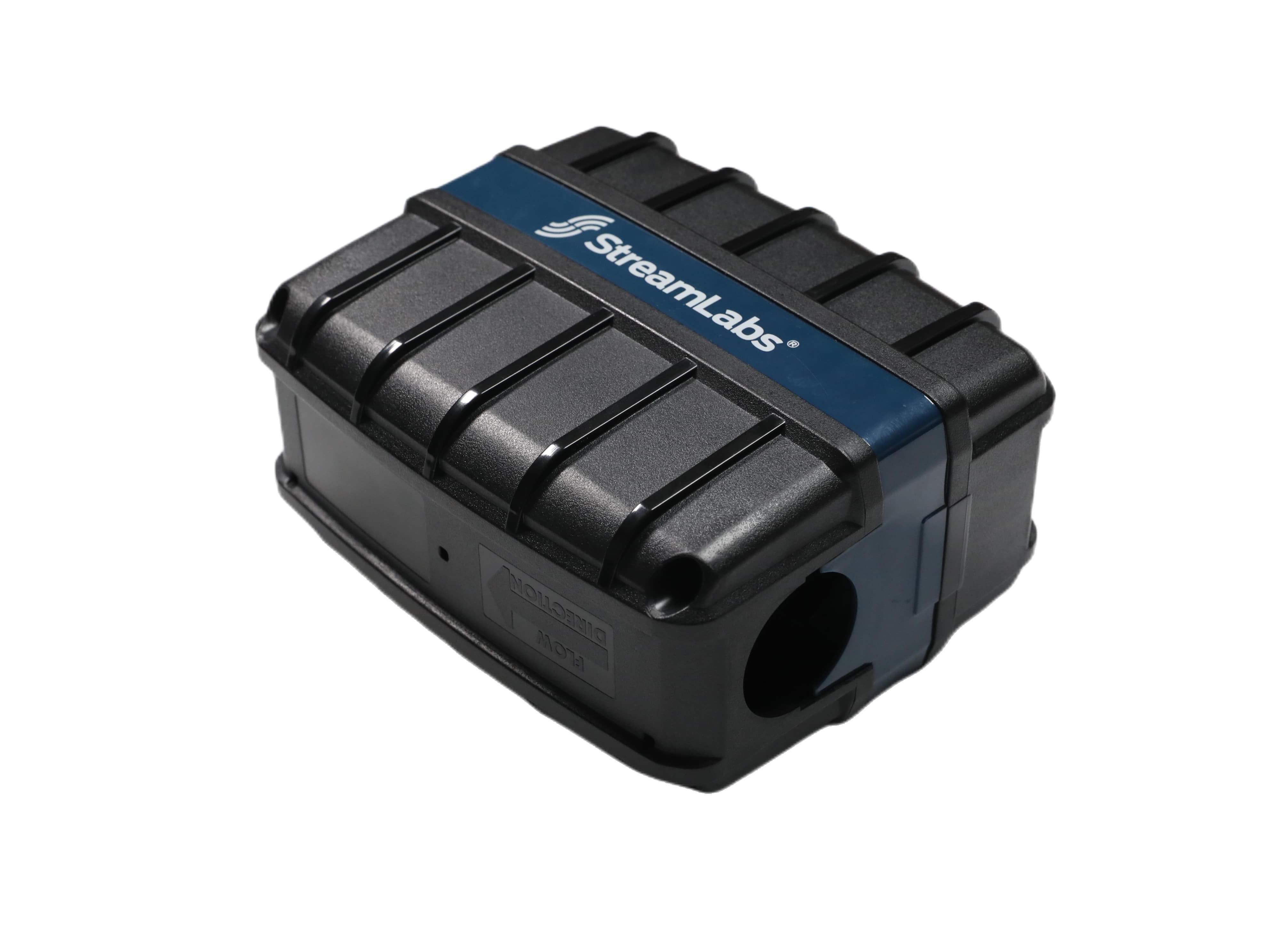
Injection molding is a manufacturing process used to create objects out of thermoplastic and thermosetting plastic materials. A variety of materials can be used, including HDPE,LDPE, ABS, nylon (or with GF), polypropylene, PPSU, PPEK, PC/ABS, POM, PMMA, TPU, TPE, TPR and more.
It involves injecting molten material into a precision-machined mold and allowing it to cool, harden, and take the shape of the die cavity.
Injection molding is a popular choice for manufacturing parts because of its accuracy, repeatability, and speed. It can produce complex parts with intricate details in relatively short timelines compared to other design processes.
Common products made using injection molding include medical devices, toys, electrical components, kitchenware, household items, automotive parts, and more.
• Flash: When the plastic exceeds the edges of the mold and forms a thin edge of excess material.
– This can be remedied by increasing the injection pressure or reducing the injection speed. It may also require a redesign of the mould itself.
• Short shot: This happens when not enough molten plastic is injected into the cavity, resulting in an incomplete and weak part.
– Increasing the plastic temperature and/or holding time should resolve this issue. It may also require a redesign of the mould itself.
• Warpage or sink marks: These occur when the part is unevenly cooled, creating uneven pressure in different sections of the part.
– This can be solved by ensuring even cooling throughout the whole part and making sure that cooling channels are properly placed where needed.
• Splay or flow lines: This defect occurs when excessive amounts of resin are injected into the mold cavity, resulting in visible lines across the surface of the finished product.
– Reducing material viscosity, increasing parts draft angles, and reducing gate size may help to reduce this type of defect.
• Bubbles/Voids: These are caused by air trapped within the resin while it is being injected into the mold.
– Minimizing air entrapment through proper material selection and gating design should mitigate this defect.
• Burrs/Pits/Sharp Corners: This is caused by a misplaced gate or too much pressure during injection, resulting in sharp burrs or corners along with visible scratches and pits on some parts.
– This can be improved by limiting gate sizes to reduce gate pressure, minimizing gate distance from edges, increasing runner sizes, adjusting mold temperatures, and slowing down filling times as needed.
• Cost-effective and efficient production of large quantities of parts in a single run.
• Precise replication of complex shapes and details.
• The ability to create custom molds for specific part designs.
• A wide range of thermoplastic materials available, allowing for unique part designs.
• Fast turnaround time due to the speed at which molten plastic can be injected into a mold.
• Little to no post-processing needed, as finished parts come out of the mold ready for use.
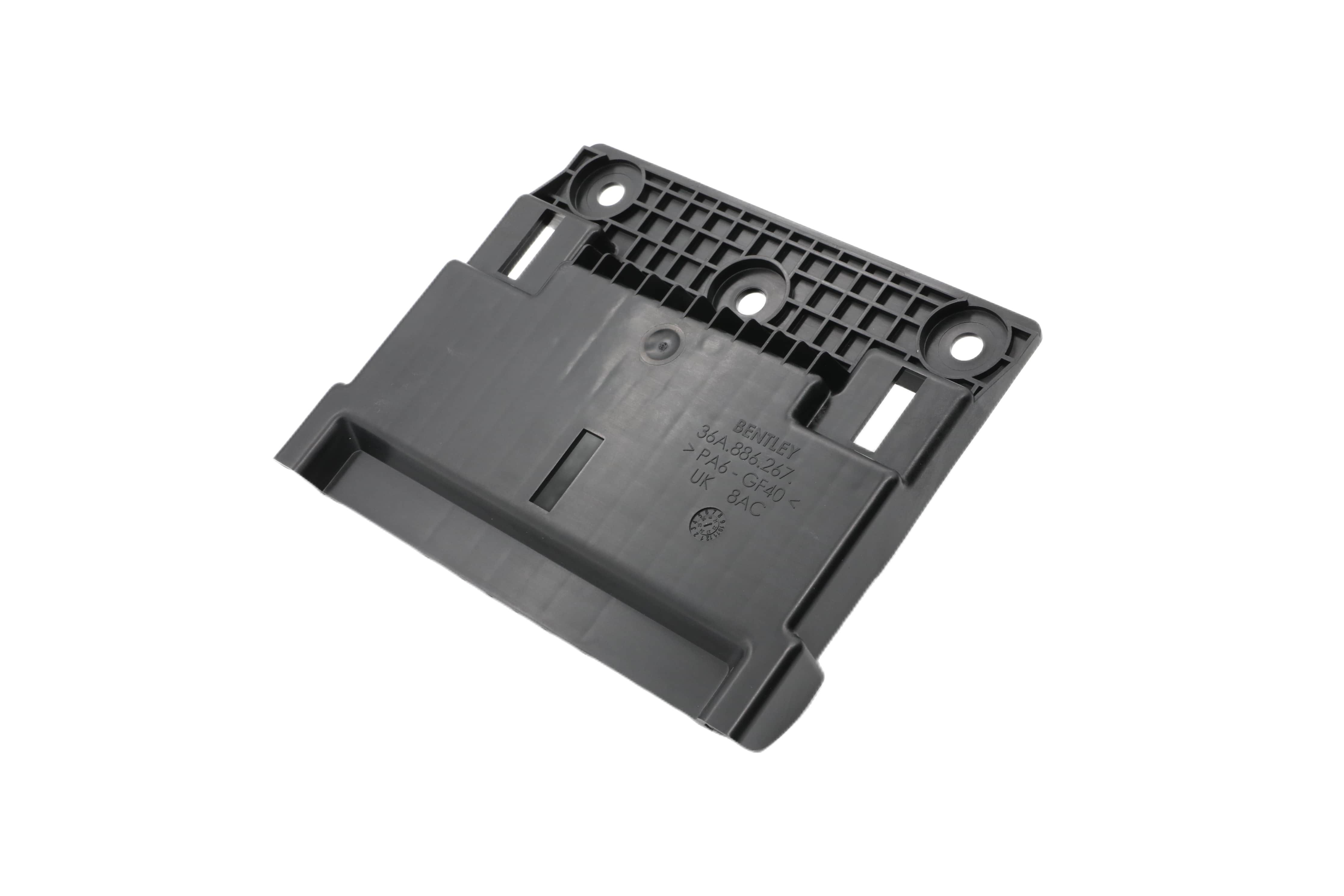
SPM has our own mold shop, so we can make your production toolings directly with low cost, and we provide free maintenance to keep your tools are in perfect status. We are ISO9001 certificated and have complete quality control workflow and full documents to make sure the consistent qualified production.
No MOQ is required for your project!

• High Initial Cost - The cost of setting up an injection molding process is usually high, as it requires a large amount of equipment and materials.
• Limited Design Complexity - Injection molding works best with simple shapes and designs, as more complex designs may be difficult to create with this method.
• Long Production Time - It takes longer to produce each part when using injection molding, as the entire process must be completed for each cycle.
• Material Restrictions - Not all plastics can be used in injection molding processes due to their melting points or other properties.
• Risk of Defects - Injection molding is susceptible to producing defective parts due defects such as short shots, warping, or sink marks.
Plastic injection molding is a common manufacturing process used to manufacture plastic products.
However, the cost of this process can be quite expensive at the beginning.
To help minimize expenses, here are some tips on how to reduce the cost of plastic injection molding:
• Streamline Your Design: Make sure your product design is both optimized and efficient so that it requires fewer materials and less time in production. This will help lower costs associated with development, materials and labor costs. SPM can provide a DFM analysis for your project by checking your part drawings, in this case, your parts will be mouldability to avoid some possible issues to cost more. And our engineer can offer technical consultation for any of your requests or problems.
• Use Quality and proper Tooling: Invest in high-quality tooling for your molds that can produce more parts in fewer cycles, thereby reducing your total cost per part. Besides, based on your annual volume, SPM can make different kinds of tools with different materials and crafts for cost-saving.
• Reusable Materials: Consider using reusable materials such as old mold base instead of new steel for your molds to reduce the overall cost if your demand quantity is not high.
• Optimize Cycle Time: Reduce the cycle time required for each part by reviewing and analyzing the steps involved and making adjustments where necessary. This can lead to significant savings over time as shorter cycle times result in fewer parts needing to be produced each day or week.

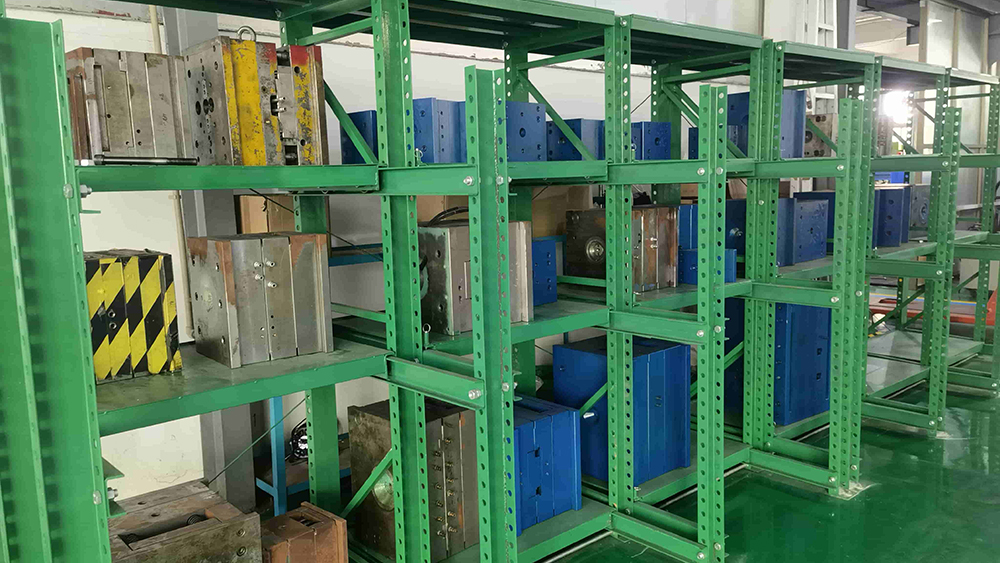
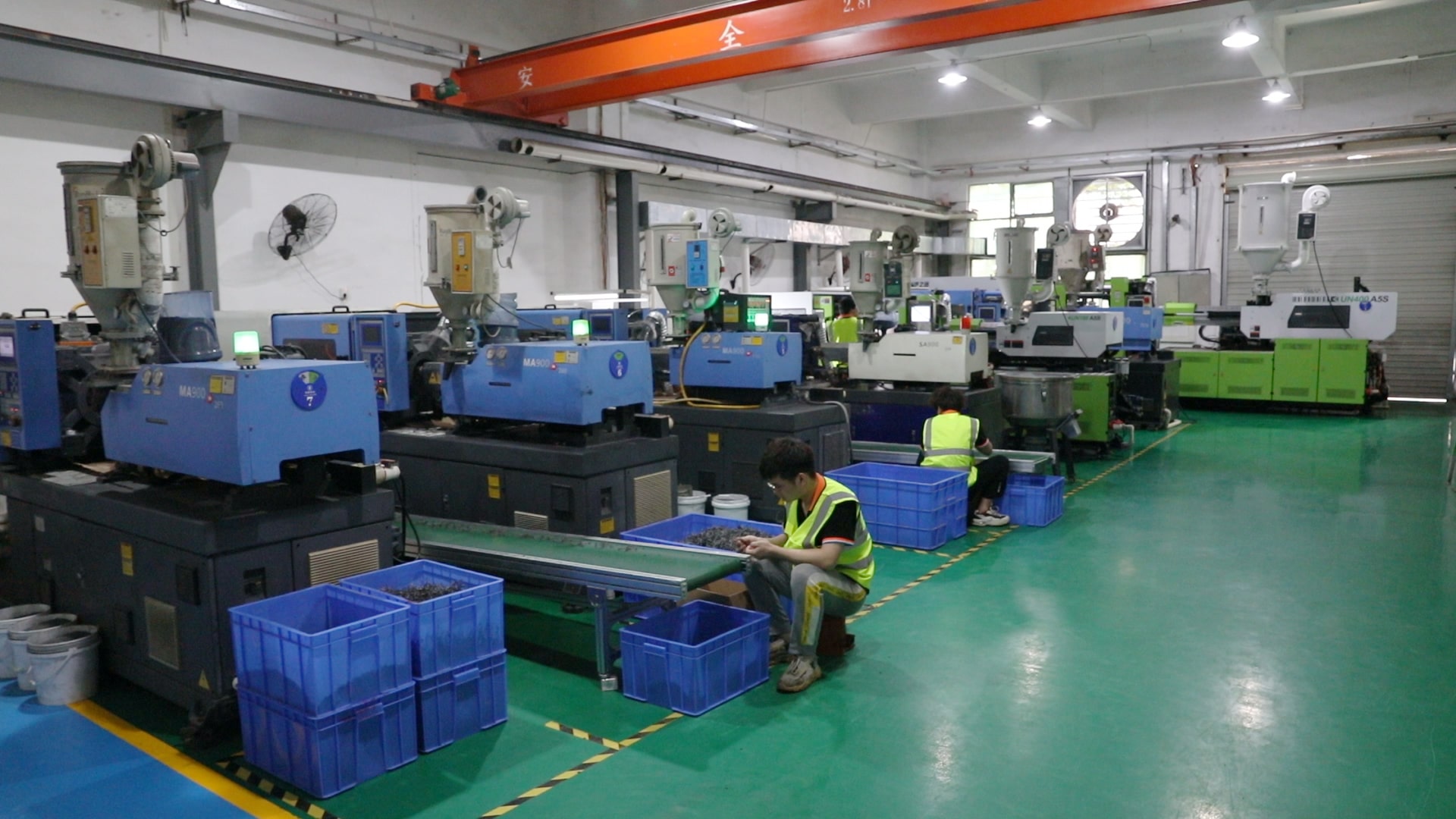
• Make production forecast: Make a good plan for the production in advance and send a forecast to the manufacturer, they can make stock for some material if their price is estimated to go higher and the shipping can be arranged by sea with much lower shipping cost instead of air or train.
• Choose an Experienced Manufacturer: Working with an experienced manufacturer who has experience in plastic injection molding like SPM can help reduce costs associated with trial and error processes as they already know what works and what doesn’t work for certain designs or materials being used in production runs
The cost of setting up an injection molding process is largely dependent on the type and complexity of the parts being created, as well as the equipment required. Generally speaking, costs may include:
• Initial Investment for Equipment - Costs for injection molds, machines, robots and auxiliaries like air compressors or installation services can vary from a few thousand to several hundred thousand dollars depending on the size of the project.
• Materials and Match Plates - Costs for materials used in the injection molding process such as plastic pellets, resins, core pins, ejector pins and match plates are usually calculated by weight.
• Tooling – Design time for molds and tooling must also be taken into account when calculating setup costs.
• Labor Costs - Labor costs may be associated with setup of the machine, operator training, maintenance or other related labor costs.
In SPM, we have experience of 3 kinds of molding services which are:
Plastic injection molding, Aluminum die cast molding, and silicon compression molding.
For plastic injection molding service, we provides rapid prototyping and on-demand manufacturing options.
The fastest lead time can be within 3 days thanks to our in house injection molding machines and with our more than 12 years of experience, we have a quick troubleshooting ability to make sure the production time.
No matter how low volume your production demand is, we can meet your requirements as to VIP customers.


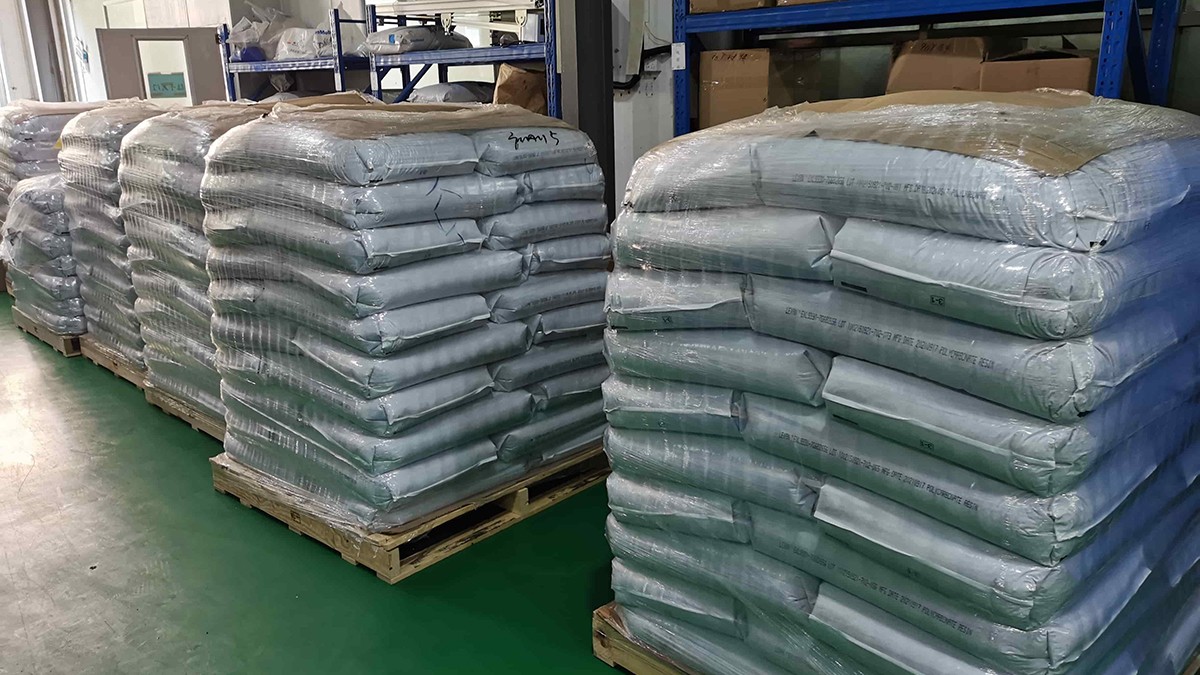
Step 1: NDA
We encourage working with Non-Disclosure Agreements before Order
Step 2: Quick Quote
Ask for a quote and we will reply price & lead time within 24 hours
Step 3: Mouldability Analysis
SPM provides complete mouldability DFM analysis for your tooling
Step 4: Mold manufacturing
Make plastic injection tooling for you as fast possible in house
Step 5: Production
Sign approved samples and start production with strict Quality control
Step 6: Shipping
Pack parts with enough protection and shipping. And Offer quick after service
They understand the importance of paying attention to details to ensure customer satisfaction. They work closely with us to design molds and dies to achieve affordable quality parts and services from concept to delivery.
Suntime acts as a single source of supply, helping to design our parts for manufacturability, build the best tools, select the right materials, make the parts, and provide any secondary operations required. Choosing Suntime has helped us shorten the product development cycle and get our products to our customers faster.
Suntime is a friendly and responsive partner, a great single source supplier. They are an efficient and experienced manufacturing supplier, not a reseller or trader company. Good attention to details with their project management system and detailed DFM process.
— USA, IL, Mr. Tom. O (Engineer lead)
I have worked with Suntime Mould for several years now and have always found them to be very professional, from the start of a project regarding our quotes and requirements, to completion of the project, with great communication thought, their English communication skills are exceptional.
On the technical side they are very good at delivering good designs and interpreting your requirements, material selection and technical aspects are always carefully considered, the service has always be stress free and smooth.
Delivery times have always been on time if not sooner, along with quality weekly progress reports, it all adds up to an exceptional all round service, they are a pleasure to deal with, and I would recommend Suntime Mould to anyone looking for a quality professional supplier with a personal touch in service.
— Australia, Mr. Ray. E (CEO)
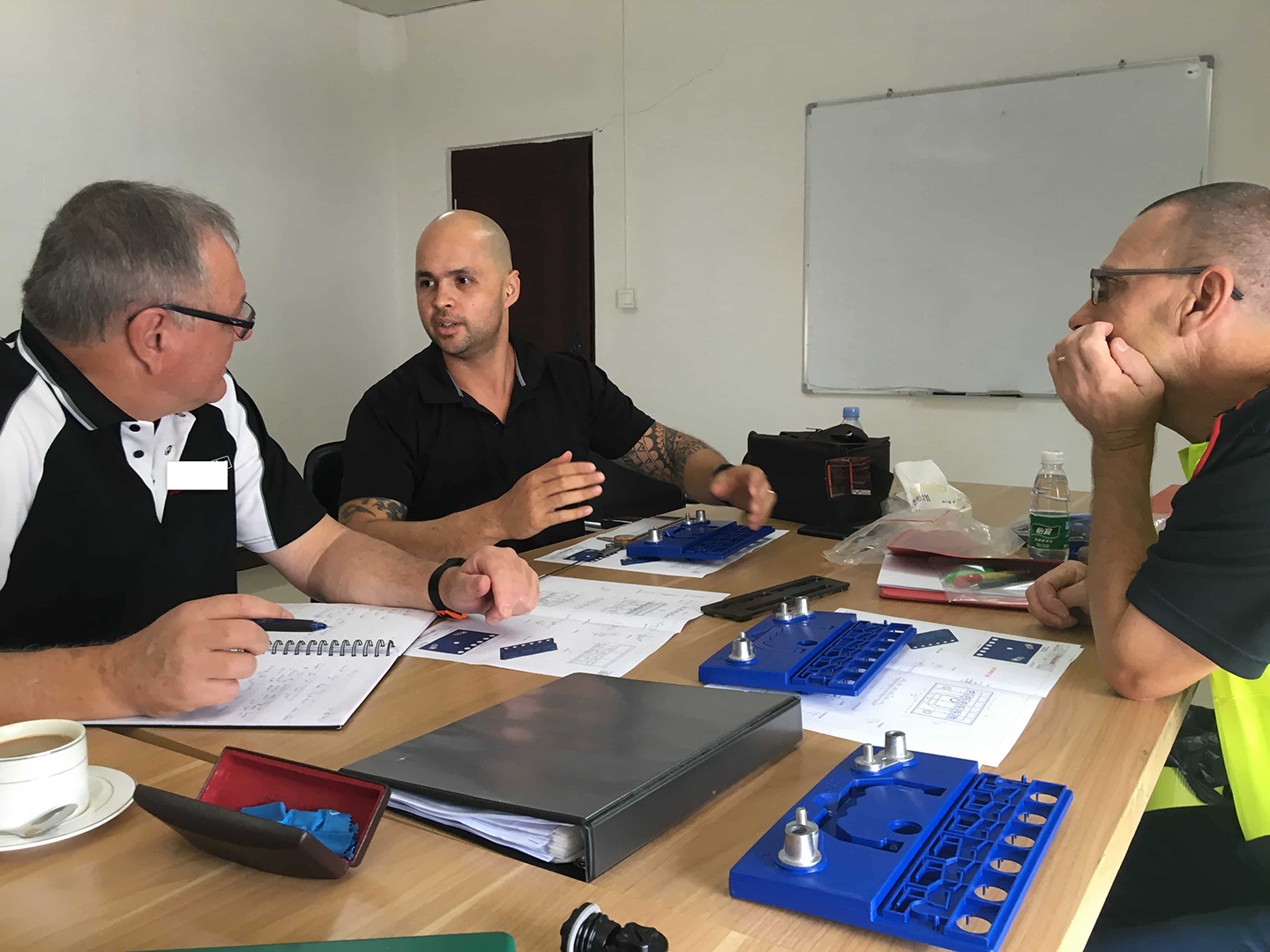
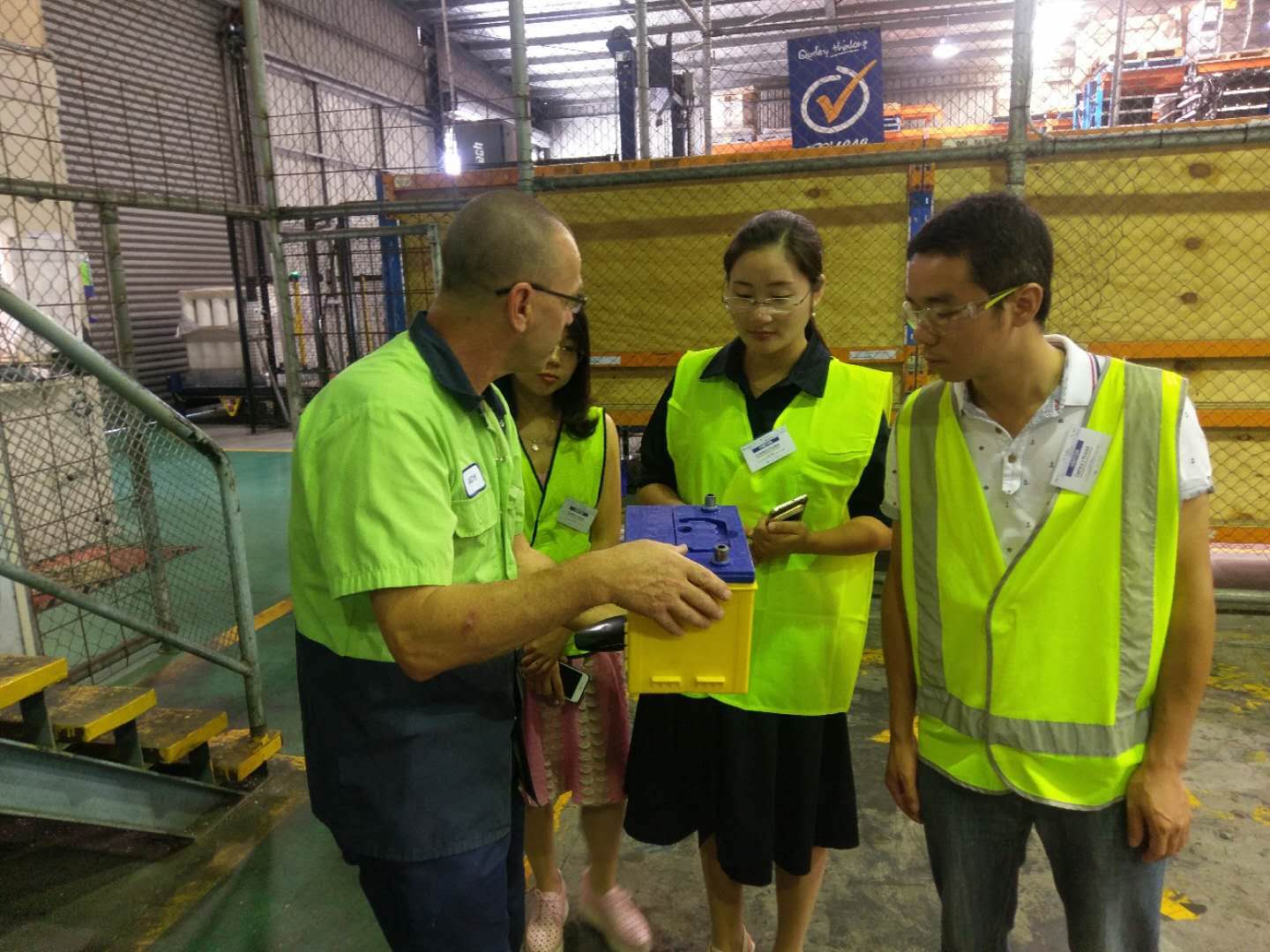
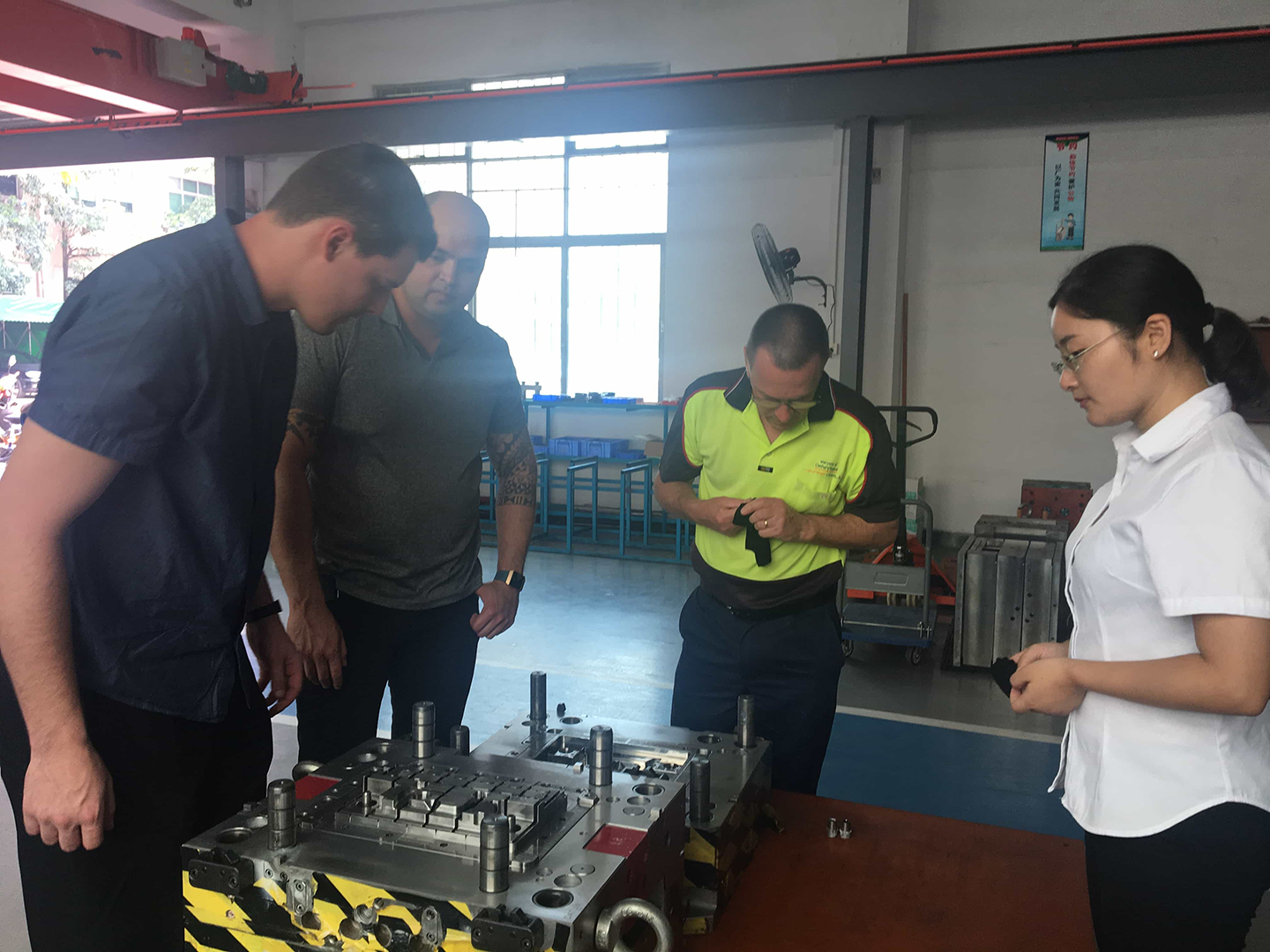
FAQ
About plastic injection molding
PC/ABS
Polypropylene(pp)
Nylon GF
Acrylic (PMMA)
Paraformaldehyde (POM)
Polyethylene (PE)
PPSU/ PEEK /LCP
Automotive
Consumer electronics
Medical device
Internet of things
Telecommunication
Building & Constructions
Household appliances
etc,.
Single cavity /Multi cavity molding
Insert molding
Over molding
Unscrewing molding
High temperature molding
Powder metallurgy molding
Clear parts molding
We have injection machines from 90 ton to 400 ton.
SPI A0,A1,A2,A3 (Mirror-like finish)
SPI B0, B1, B2, B3
SPI C1, C2, C3
SPI D1, D2, D3
CHARMILLS VDI-3400
MoldTech texture
YS texture
Yes, we are ISO9001:2015 certificated manufacturer
Yes, besides plastic injection molding, we also have made parts of silicon rubber for customers
Yes, we also have much experience of making die cast mold and production for aluminum die casting parts.
In DFM, we provide our analysis including angle drafts, wall thickness (sink mark), parting line, undercuts analysis, welding lines and surface issues, ect,.